2023-09-01
The advantages of an electroformed mould include complex shapes. The negative image of a mandrel is used to create the electroform. This process can produce both flat and 3D parts. The same process is used in the manufacture of CDs and DVDs, where a nickel stamper creates a unique pattern of submicron-sized pits that encode the content for the player. A number of other industries use electroformed nickel stampers to manufacture specialized parts.
This process allows for complex shapes and high accuracy. As the form touches the mandrel, the surface is extremely accurate. The outside area will be thicker, so it will lose definition. It is possible to create a thicker object using this process, but the material will lose definition. In addition, the outside surface will be more porous than the inside. The resulting metal object will have an uneven surface. In this case, the metal insert may be too thick or too thin, and this will result in a higher cost.
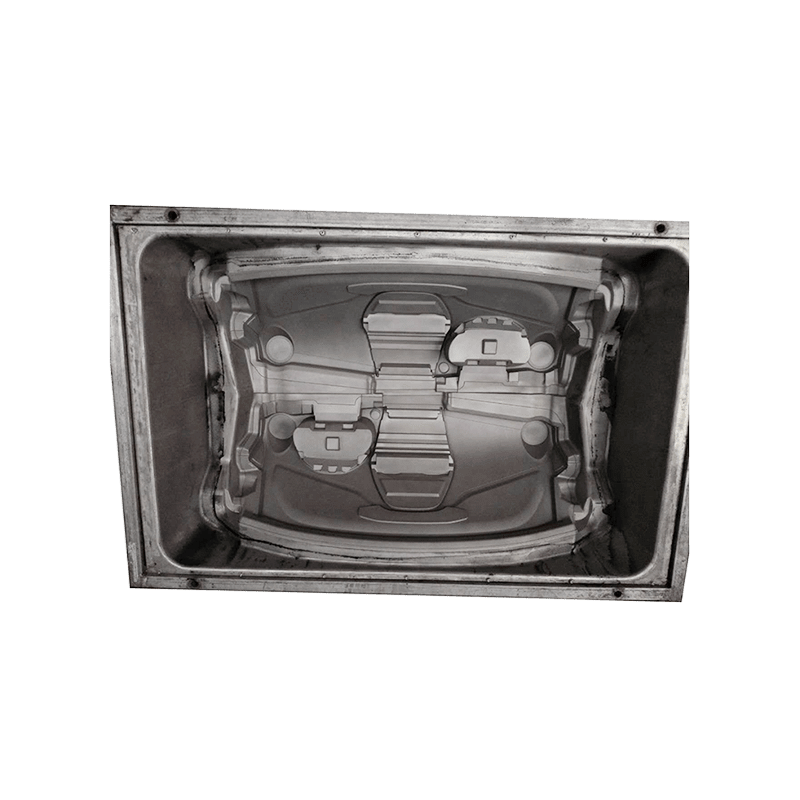
Another advantage of electroforming is its thermodynamic efficiency. The metal used to make an electroformed mould is copper, which is a good choice for optical applications. It can also be useful for joining two components. The electroformed object is often plated, increasing its quality and properties. An electroformed mould is often less precise than the interior one. Its outer surface will have a more rougher texture than the inside surface, which means it will lose definition. In addition, it can also have excess material on its edges and corners. To remove this unwanted material, the electrodes can be etched or drilled out.
The electroformed mould is a good option when the precision is important. A mould that is perfectly proportioned will have a higher quality surface than a mould that has been electroformed using a more expensive method. The latter is also a good choice for complex true geometric shapes with thin walls. It is an excellent option for high repeatability. And as with all other types of abrasive materials, it is easy to etch the surface.
An electroformed mould will have an extremely high quality finish. The metal used will have a smooth surface with no imperfections. The metallic insert will have a smooth surface and an electroformed mould will be able to resist heat. However, an electroformed mould is not a perfect match for all materials. A good example of an electroformed mould is one where the material is not too thin. It may have a thin wall, but it is too thick to support the plastic.
In some cases, an electroformed mould may not be entirely solid, but instead be a hollow core. Nevertheless, it is better to electroform a metal mold in order to achieve the desired result. This method has several advantages. It is the only way to get a metal insert in a metal object. Moreover, it is a more precise way to make a complex object. The process can be very expensive, so make sure you take a look at the different options.
An electroformed mould is a thick shell that is a few millimeters thick. The shell must be electrically conductive. Then, it must be backed up with a suitable material. The thickness of the mould is dependent on the density of the current. The process of electroforming can also be categorized into two types: plating up and mold-release methods. In addition, an electroformed mould can be incorporated with other components.
A two- to three-mm thick electroformed nickel mould can have early cracking when exposed to thermal load cycles. The investigators obtained monotonic properties of electroformed nickel at various temperatures and identified the underlying causes of fatigue. Then, they used finite element modelling to analyze the mold. They discovered that overconstraining in service resulted in excessive thermal stresses, which led to an accelerated crack initiation. They also proposed several remedies to prevent failures.