2023-09-01
Electroforming is a sophisticated manufacturing process that involves the precise deposition of metal layers onto a master model to create a mold. Electroforming PDCPD Mold technology leverages this process to generate intricate molds using PDCPD as the substrate material. The process begins with the creation of a master model, often made using rapid prototyping techniques or traditional machining. This model is coated with a conductive layer and immersed in an electrolytic bath. Through controlled electrodeposition, metal layers gradually form on the master model's surface, replicating its intricate details. Once the desired thickness is achieved, the metal-coated model is removed, leaving behind a precise and intricate mold that can be used for PDCPD injection molding.
Precision Redefined: The Art of Electroforming PDCPD Molds
Precision is a defining attribute of Electroforming PDCPD Mold technology. The electroforming process allows for the creation of molds with sub-micron accuracy, faithfully reproducing even the most intricate features of the master model. This level of precision is particularly crucial in industries where complex geometries and fine detailing are essential. Electroforming PDCPD Molds redefine what is achievable, enabling manufacturers to produce components with impeccable accuracy and consistency.
Customization Unleashed: Design Freedom and Complexity
The marriage of electroforming and PDCPD opens up unprecedented avenues of customization and design complexity. Electroforming PDCPD Mold technology empowers designers and engineers to create intricate and unique molds that capture every nuance of their vision. From automotive components with complex textures to finely detailed medical devices, this technology enables the production of products that were once considered challenging or even impossible to manufacture.
PDCPD's Unique Properties: A Marriage of Strength and Design
PDCPD, known for its exceptional mechanical properties and durability, serves as the substrate material in Electroforming PDCPD Molds. This unique combination of electroformed metal and PDCPD offers a balance between strength and design flexibility. The metal layer ensures structural integrity and precision, while the PDCPD component contributes to the final product's durability, chemical resistance, and lightweight nature.
Applications Across Industries: A Multifaceted Solution
The versatility of Electroforming PDCPD Mold technology is evident in its applications across a wide range of industries. In the automotive sector, it facilitates the production of intricate grilles, emblems, and interior components. In aerospace, it contributes to the creation of lightweight and aerodynamic parts. In the realm of consumer electronics, it allows for the manufacturing of intricate and visually appealing casings. From luxury goods to medical equipment, this technology offers a multifaceted solution that caters to diverse industry needs.
Sustainability and Efficiency: A Greener Approach
Electroforming PDCPD Mold technology aligns with sustainability goals by promoting efficiency and minimizing waste. The precision of the electroforming process ensures minimal material usage, reducing waste and resource consumption. Additionally, the durability and longevity of PDCPD-injected components contribute to extended product lifetimes and reduced replacement needs.
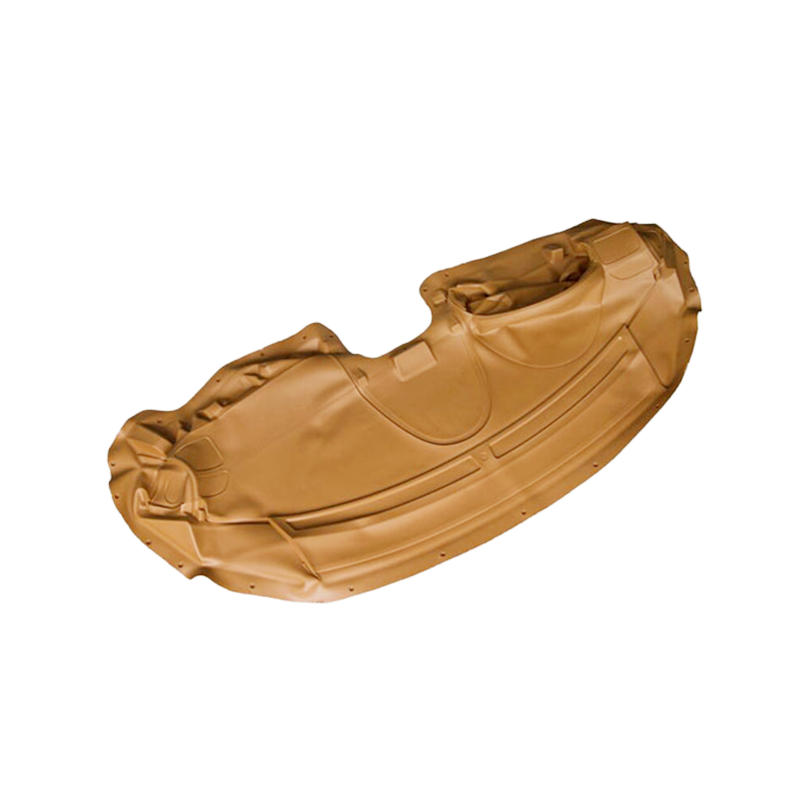