2023-09-01
The process of RTM moulding is performed at room temperature or can be heated. If fast cycle times are required, heated moulds are required. After the part is finished, the mold is inspected for defects, and the reinforcement is placed inside the mould. The resin is injected under pressure and is cured in the mold. The resin is cooled in the mold and is then cured in the mould. When the part is finished, it is removed from the mould.
The process of RTM mould fabrication requires a high level of technical knowledge. The RTM process produces high volumes of finished parts, so it's critical to make sure your tooling has multiple release capabilities. If the release agent is insufficient, it'll need to be touched up too often, which results in a build-up on the tool surface and difficulty in extracting the parts. Excessive application of the release agent will make the process more difficult and lead to higher material costs.
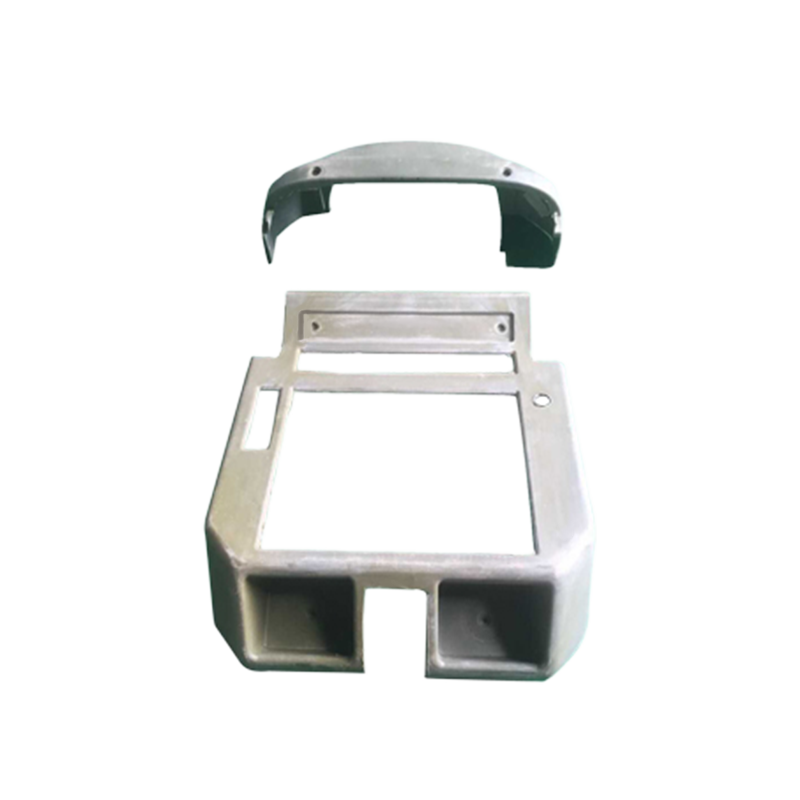
A wide variety of materials and design options are available. RTM is a cost-effective option for many industries. For example, the use of polymers in composite parts allows manufacturers to reduce production costs. And because the resin has a relatively low density, it is highly resistant. The process is also flexible, enabling them to produce even the most complex shapes. It also saves labour by eliminating the need for expensive PVA coatings or wax.
The process of RTM moulding uses a liquid thermoset resin system to build an FRP part. The preforms are layers of dry fabrics that serve as the preforms. The resin is injected into the mold to produce the final shape of the part. This process allows a single piece to be constructed without the need for separate pieces. This makes it a highly efficient option for manufacturers of FRP products.
RTM moulds are highly versatile and flexible. They are ideal for making thin or small parts. They can be used for a variety of purposes, from prototypes to high-volume production. However, open cell core parts may not be viable for RTM. Further, open cell core parts require highly specialized equipment and can be difficult to process. For example, the process may not be suitable for small and lightweight components. The complexity of a mould's design can cause it to break.
An RTM mould is a very flexible and efficient way to make moulds. Its versatility allows it to be used for a variety of applications, and has a number of advantages. A good RTM mould has the capacity to produce a large number of different parts, even if the end result is very small. The advantages of RTM are the ease of use, low cost and high quality. You will have a high-quality product with low reject rates.
The RTM process is a rapid manufacturing method that produces finished parts with high fibre content. It is crucial for high-quality plastic parts. In some cases, the process requires a high speed of processing. Some of these moulds have to be highly complex, while others are simple and affordable. These are essential for the creation of high-quality plastic parts. If you are planning to use RTM moulds, it is important to invest in the proper tools and the right process.
For fast cycle times and high quality RTM parts, it is important to use a high-quality RTM mould. A high-quality RTM mould will have two finished surfaces and will last for many years. If you want to make a custom part, it will be more affordable than a custom RTM. And you'll get a much better product in no time. With an accurate mold, you can create the part you need.