2023-09-01
The Electroforming process is very effective and provides a number of advantages. The PDCPD mold can be molded to different cross-sectional thicknesses, reducing cycle time. It also helps in minimizing phantom lines. The process also allows for the design of a variety of parts and materials, including unpainted and painted materials. In addition, the molded part can be coated with special materials.
The main benefits of PDCPD molds are their chemical resistance, good tensile properties, and high impact resistance. In addition to these advantages, they can also be processed with other materials, such as steel, aluminum, and composites. For example, this process works well with the aluminum PDCPD mold. If you need a large electroforming mold to produce wind turbine or auto parts, this method is an excellent choice.
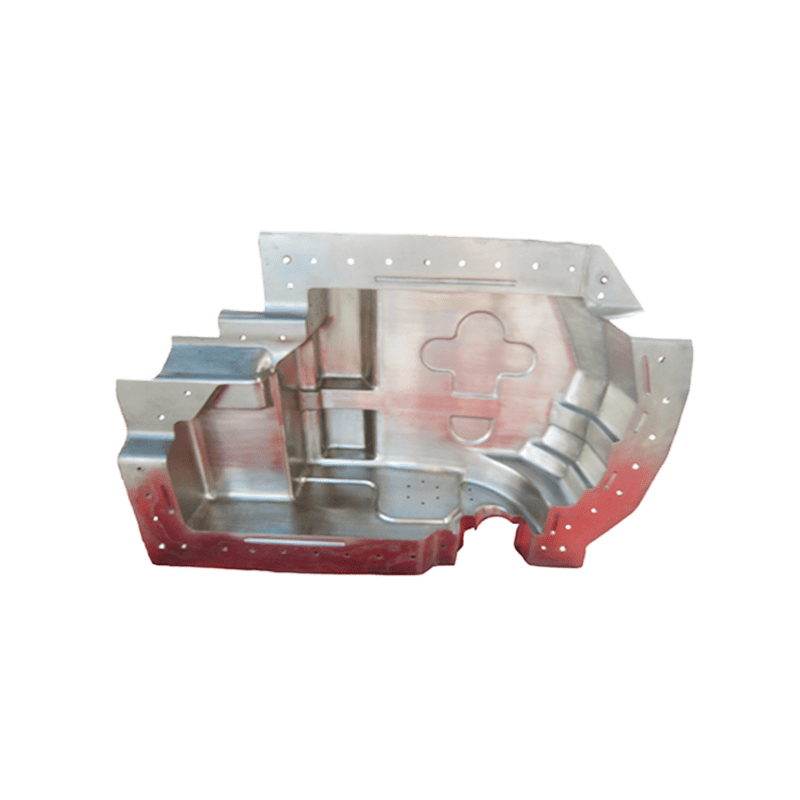
This process is extremely versatile. A large mold must be placed in an EDM dielectric tank next to another solid piece of metal. The solid piece of metal also holds the wire. The electrodeposition solution then forms the plastic in the mold and coats it. The completed object is then removed from the electroforming machine. The result is a high-quality product with a great aesthetic value. If you need a mold with this high precision, consider the electroforming process.
The basic process involves using a mold with a wire attached. Once the mold is placed in the plating solution, the solid piece of metal next to the mold is a solid piece of metal that also holds a wire. When the mold is immersed in the electroforming solution, the metal forms within the mold and coats the mold. Once the metal hardens, the finished product is removed. If the metal is applied properly, the object is a perfect replica.
This process is based on the concept of electroplating. The metal is coated over the mold and the resulting object is a metal object. However, unlike electroplating, electroforming uses different methods. For instance, it can be used in plastic objects that are a few inches wide. The metal coats the mold, while the mold is in the metal solution. The final product is then removed from the electroforming process.
A PDCPD mold uses the principle of electrolytic deposition to replicate complex shapes. It was first invented by a Russian scholar B.S. The mold's original use was to reproduce printing plates and metal artwork. Record stampers were the first industrial products to use the electroforming process. Its versatility made it a popular technology for a wide range of industries. There are many applications of this type of patented tool.
Electroforming a PDCPD mold is a process that uses the principle of electrolytic deposition to duplicate complex shapes. It is a unique application of electroplating and was developed by a Russian scholar in 1837. The electroforming process was initially used to reproduce printing plates and metal artwork. But later on, this method was also used to manufacture record stampers. These devices are widely used in a variety of industries, from automobiles to consumer electronics.
Electroforming PDCPD molds are the basis of electroforming. These molds are made of nickel and are made from the same material as the original mold. The original material can be gypsum, wax, stainless steel, and aluminum. The mold is usually insulated and can be electroformed with fibers. Moreover, it is compatible with steel, aluminum, and composite molds. Once the molding process is complete, the final product is ready to be installed in various types of applications.
The PDCPD mold is made from nickel and copper. A thin layer of nickel alloy is used as the cavity wall of the mold. The thick layer of copper is used to back the mold. The two metals are connected by wire. The entire process involves a battery and the electrode. Then, the metal will coat the mold. The finished object will be finished. When the process is complete, the electroformed object will be removed from the mold.