2023-09-01
* RTM molding can be performed at room temperature. The process can also be performed at elevated temperatures. The mould is heated if it needs to be used at a high-speed and for consistency. During the injection process, the reinforcement is placed in the mould and the resin is injected under pressure. After the injection is completed, the part is cured inside the mould. This allows the resin to cure properly and forms the final part.
* RTM has many benefits. In addition to being economical and efficient, it is a cost-effective process. Its main drawback is that the permeability of the materials is dependent on the pore space of the mould. Several factors contribute to the permeability of a given material, including the pore space, pressure gradient, and bed dimensions. Therefore, RTM moulds are highly flexible, reduce mould cost, and reduce lead times.
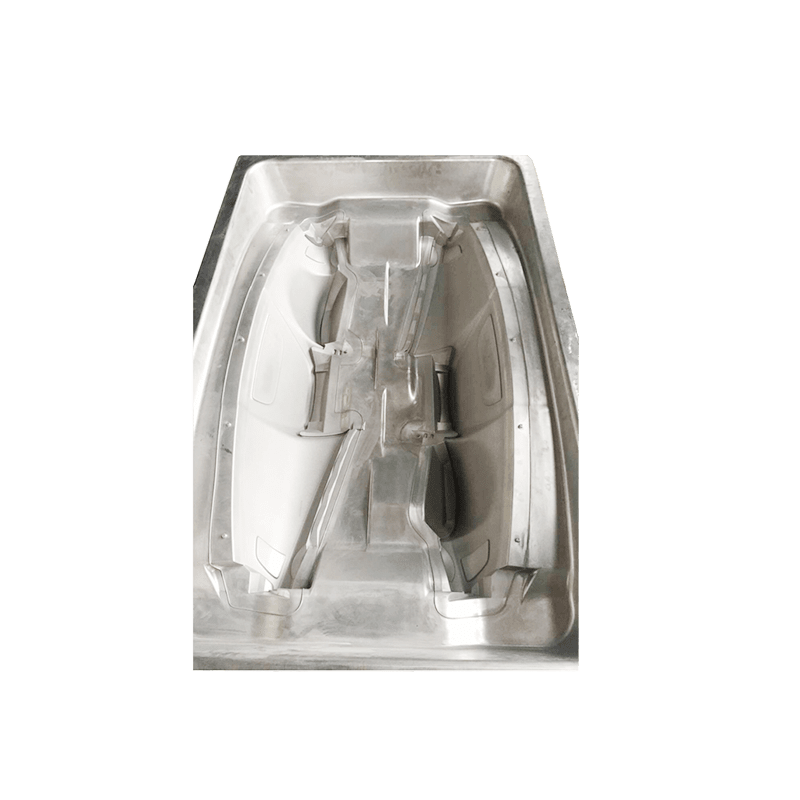
* It has a low porosity. Its surface finish is good. It is also compatible with various types of resin. A UD-CSM combination is the most popular. It is a mould with a needled or stitched mat. A UD-CSM configuration is used for hot moulds. It has several advantages. Its high viscosity reduces the risk of void expansion and it has a lower pressure than a conventional resin-casting process.
Another advantage of RTM mould is the lower cost. It is less expensive than other types of plastics and is suitable for low-volume applications. Moreover, it is very versatile. It can be used for a wide variety of applications, from high-end products to prototypes. It also reduces the cost of a mould. It is a versatile technology. It is easy to learn and utilise. There are many advantages of an RTM.
A proper RTM mould will reduce the costs and time involved in production. It can also reduce scrap and reworked components. In addition, a well-designed tooling will determine the geometry of the part. Furthermore, it will control the flow of resin. If the preform is not designed correctly, the part will not be suitable for the product. Once the mould is prepared, it is ready to be used. If it has been designed properly, RTM will result in a durable and reliable product.
RTM moulds can reduce the amount of scrap and reworked components. The geometry of a part is determined by the RTM mould. It also controls how much resin is added to the part. It can be customised for a variety of different applications. It is ideal for composites, including plastics. And because it is customized, RTM moulds can be adapted to meet your needs. In the process of RTM, an RTM mould can be modified to suit any part.
RTM is a process that is very fast. The process uses a heat-treated mold to reduce the time it takes to complete a single part. A properly-designed RTM mould can reduce the number of reworked parts and minimize scrap. Once a part is cured, the mould can be opened. A skilled technician will remove the part. They will have no problems with the RTM mould. There are no other limitations.
The RTM process requires a high-quality RTM mould. It is a great choice for producing composite parts. This technique is quick and efficient, and is a cost-effective way to produce high-quality composites. The RTM process also offers many advantages. For one thing, it can reduce scrap. A poorly-made mould will not be as durable and will not be as strong as it could be if it is fabricated using RTM technology.
An RTM mould is a matched metal tool that allows the resin to be injected into a preform. This mould will have dedicated vents for vacuuming the part. The resin will enclose the part, making it ready to open. A quality RTM mould will be a great asset to your business. In addition to these features, it will also help you save time. With these two benefits, you will be able to boost your efficiency and reduce scrap.