2023-09-01
One of the key advantages of DCPD molding is the exceptional strength and durability it imparts to components. The resulting parts exhibit outstanding mechanical properties, including high stiffness and impact resistance. DCPD-based components are known for their ability to withstand harsh environmental conditions, making them suitable for a wide range of applications in industries such as automotive, aerospace, and construction. The exceptional strength and durability of DCPD-molded parts ensure longevity and reduce the need for frequent replacements, leading to cost savings and increased operational efficiency.
DCPD molding enables the production of components with complex geometries and design freedom. The liquid nature of DCPD allows it to flow into intricate mold cavities, ensuring precise replication of even the most intricate details. Manufacturers can leverage this capability to create parts with complex shapes, undercuts, and thin walls. The design freedom provided by DCPD molding opens up new possibilities for innovation and allows manufacturers to optimize the performance and functionality of their components.
In addition to its strength and durability, DCPD molding offers the advantage of lightweight components. DCPD resin has a low density, resulting in parts that are significantly lighter compared to those made from traditional materials such as metal. The lightweight nature of DCPD-molded components is especially valuable in industries where weight reduction is crucial, such as automotive and aerospace. Lighter components contribute to improved fuel efficiency, enhanced maneuverability, and increased payload capacity, ultimately leading to better overall performance and reduced environmental impact.
Another notable benefit of DCPD molding is the inherent chemical and corrosion resistance of DCPD-based components. DCPD resin exhibits excellent resistance to a wide range of chemicals, including solvents, acids, and alkalis. This makes DCPD-molded parts suitable for applications where exposure to aggressive substances is common. Furthermore, the corrosion resistance of DCPD-based components ensures long-term reliability and reduces the risk of damage or failure in harsh environments.
DCPD molding offers an efficient production process that contributes to increased productivity and reduced manufacturing costs. The low viscosity of DCPD resin allows for fast and consistent injection into the mold cavity, minimizing cycle times. The thermosetting nature of DCPD ensures rapid curing, enabling shorter production cycles compared to other molding processes. The efficiency of DCPD molding translates into higher production volumes, reduced energy consumption, and improved overall manufacturing efficiency.
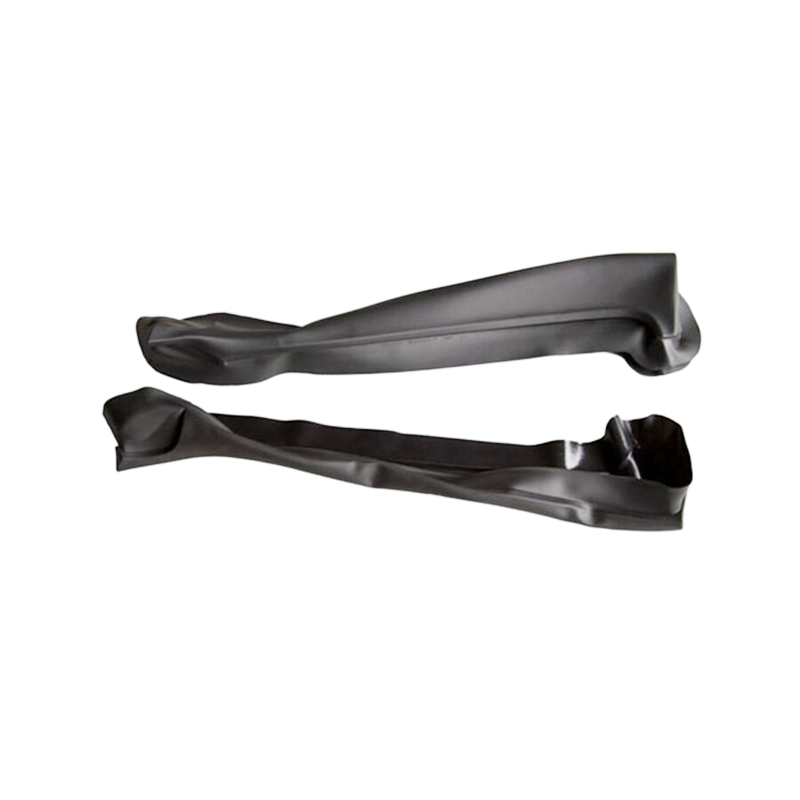