2023-09-01
The electroform is then bonded to a tool steel block and brought to its finished dimensions. The resulting mold insert has a high thermal conductivity envelope around each cavity, which effectively sucks heat away from the cavity walls. This makes it possible to make electroformed injection molds with integrated cooling.
The DCPD mold is a great solution for large composite fiberglass parts. This process is similar to Resin Transfer Molding, but with two molding surfaces. The parts produced with DCPD are lightweight and strong. Its flexibility makes it possible to design complicated parts with this technology. DCPD molds are used for a variety of industrial applications, including the production of fenders and hoods for massive transport trucks.
Compared to other types of molds, this mold is inexpensive and easy to produce. It allows you to produce unique shapes and sizes, which will help your products stand out from the crowd. A customized PDCPD mold can be used for different applications. A custom mould can be customized with a unique shape or a complex surface.
When electroforming PDCPD molds, it is important to keep in mind the fact that the mold flux can vary in its melting process. The melting process of the mold flux plays a significant role in determining the contact angle. As a result, the final contact angle for Flux1 in a 20-mm thick mold is lower than that of the other two cases. This is due to intensive interracial reactions that occur near the interface.
The use of surfactant agents is important for the best moldability characteristics of the material. This technique helps control the temperature and speed of the mould. In addition, it enables multiple material shots to be added without stopping rotation. This technique has recently gained renewed industrial interest. The future of this process is bright with endless possibilities.
A custom mould allows a business to produce unique products. It also reduces manufacturing errors. Moreover, a custom mould is easier to create than a standard one, which saves time and money. Increasing the speed of production can translate to higher revenue. Finally, a custom mould can provide a personalized look for the product.
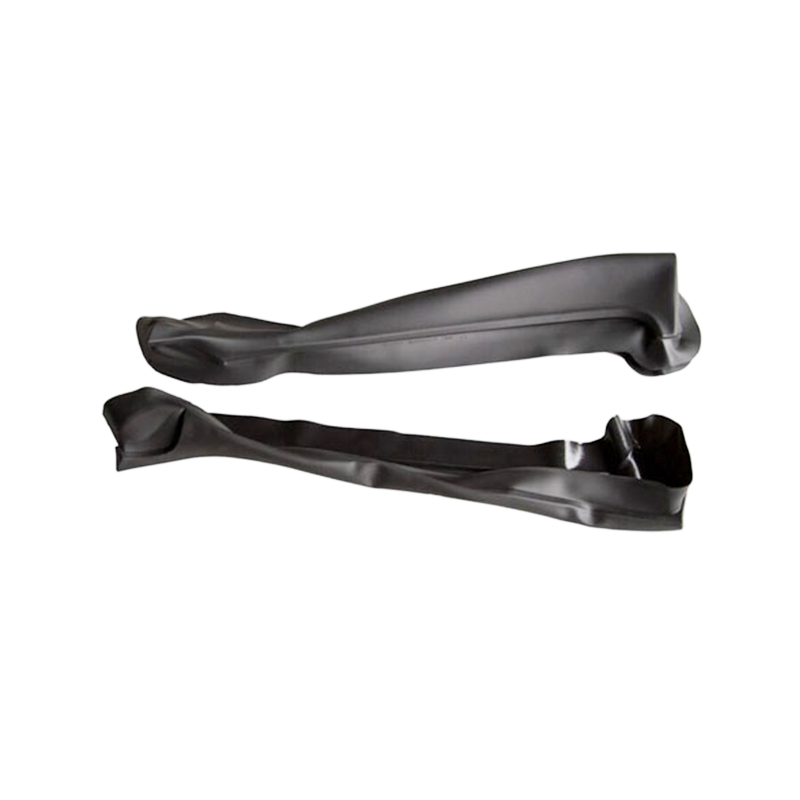