2023-09-01
RTM mold technology has been gaining popularity in recent years due to its many advantages over other manufacturing processes. For example, it offers excellent surface finish, dimensional accuracy, and allows for the production of large, intricate parts with minimal waste. In addition, the RTM process is more environmentally friendly compared to other traditional methods such as injection molding, as it produces less waste and consumes less energy.
One of the primary benefits of RTM mold technology is its ability to create high-strength, lightweight composite components. This is particularly important in the aerospace industry, where weight savings can translate into significant fuel savings and lower operating costs. RTM molds can be used to create structural components for aircraft, such as wing spars, fuselage sections, and engine nacelles, which are strong enough to withstand the extreme loads and stresses of flight while remaining lightweight.
The automotive industry has also embraced RTM mold technology, as it allows for the creation of lightweight components that improve fuel efficiency and reduce emissions. RTM molds can be used to create body panels, chassis components, and other structural parts that are strong, durable, and have excellent dimensional stability.
In the marine industry, RTM mold technology has been used to create high-performance composite components for boats and yachts. These components are lightweight, corrosion-resistant, and have excellent impact resistance, making them ideal for use in harsh marine environments.
Despite its many advantages, there are also some challenges associated with the use of RTM mold technology. One of the main challenges is the high cost of the tooling required to produce the molds. RTM molds are typically more expensive than other types of molds, which can make it difficult for smaller companies to adopt the technology.
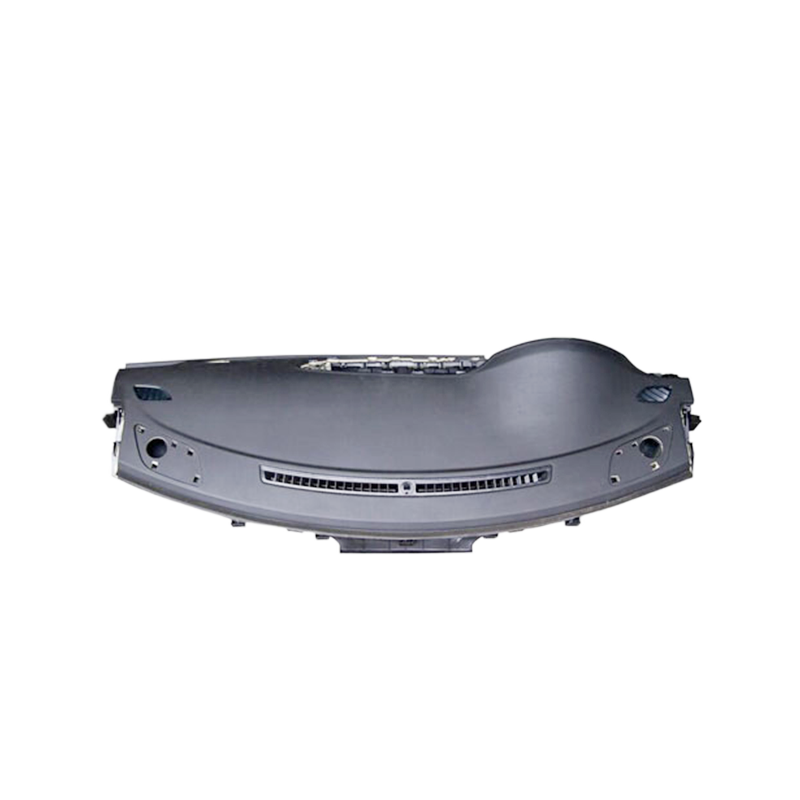