2023-09-01
RTM molds have several advantages over traditional molding methods such as injection molding and compression molding. The most notable advantage is speed. RTM molds can produce parts in a fraction of the time it takes with other molding methods. This speed has the added benefit of reduced costs, as manufacturers can produce more parts in a shorter amount of time, lowering their overhead costs.
RTM molds also offer greater design flexibility than traditional molds. The resin used in the RTM process can be formulated to meet specific strength, stiffness, and weight requirements. This means that manufacturers can produce parts with a wide range of properties, making it possible to produce complex and intricate designs with ease.
Another advantage of RTM molds is the high-quality surface finish of the final product. The closed mold environment allows for complete control of the curing process, ensuring that the final product has a uniform and consistent surface finish. This is especially important for applications where appearance is critical, such as in the automotive and consumer goods industries.
The use of RTM molds is not limited to any particular industry. The process is widely used in the automotive, consumer goods, aerospace, and sporting goods industries. For example, the automotive industry uses RTM molds to produce parts such as body panels and structural components, while the consumer goods industry uses them to produce products such as household appliances and electronic devices.
Despite the many advantages of RTM molds, there are also some challenges associated with the process. The most significant challenge is the high cost of the molds themselves, which can be several times more expensive than traditional molds. Additionally, the process requires a high level of technical expertise to ensure that the molds are properly designed and the resin is properly formulated.
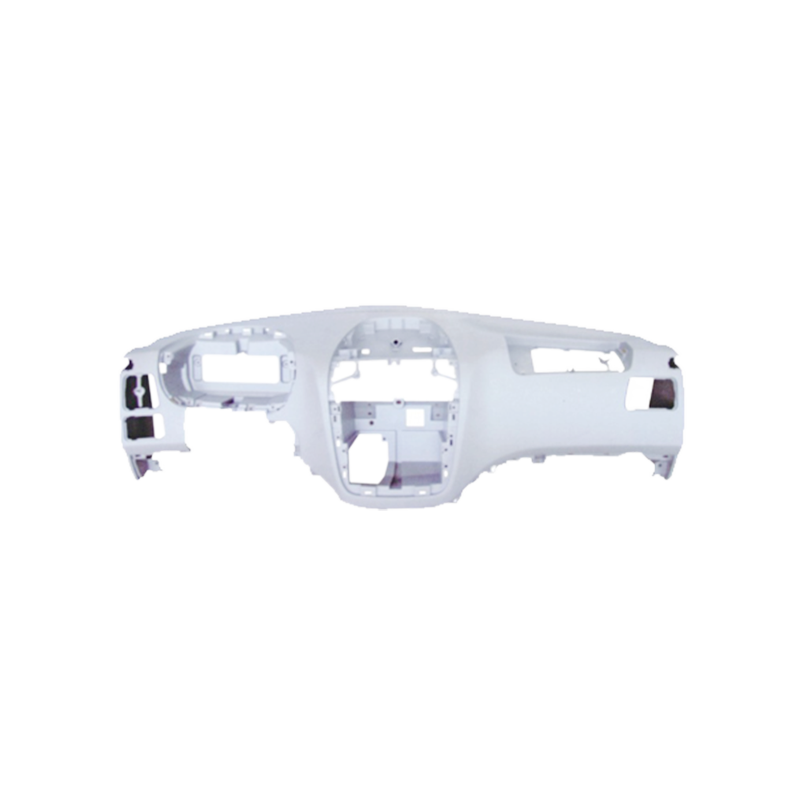