2023-09-01
The height of the form plate depends on the dimensions of the part and platen. The maximum mold height is determined by the daylight range of the resin. Minimum mould height is limited by the opening stroke of the mold carrier. The form plate's height is dependent on the geometry of the product, and whether auxiliary elements are required for the part production process. There are two main industrial strategies used to define the dimensions of the form plate. These are UD-CSM combination moulds and needled mats.
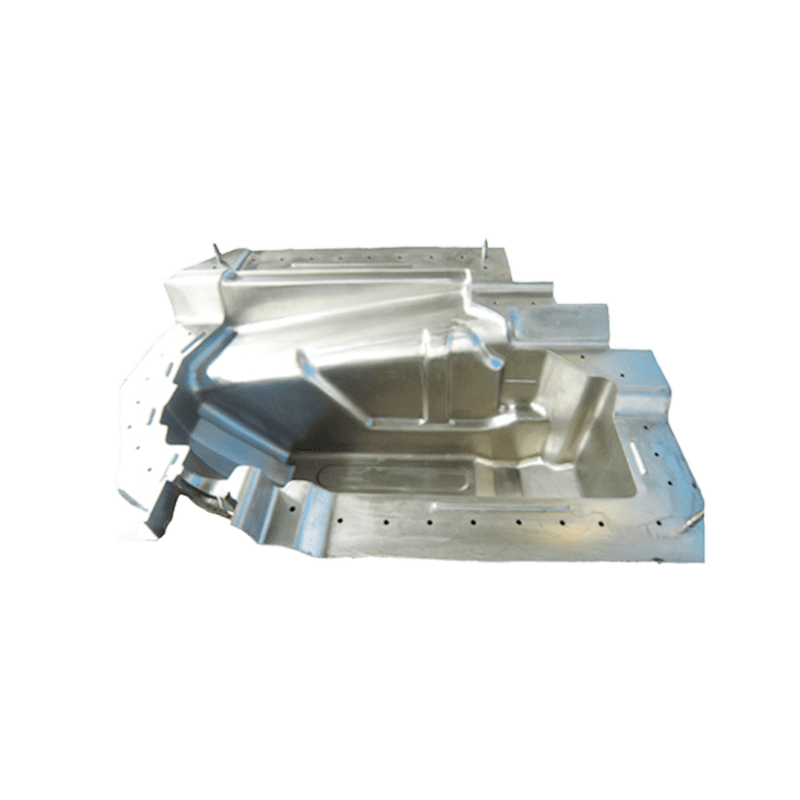
The process of vacuum molding requires the degassing of the resin before it is poured into the mould cavity. Then the resin is reinforced with a layer that will minimise the amount of time the mould remains open. This preforming reinforcement may involve a number of methods, but usually involves the use of a binder to hold the layers in place while the resin flows through the process. The cost of the preforming material is estimated at 70 percent of the total cost of RTM components.
The RTM process is similar to conventional injection molding, except that the process uses low-viscosity thermoset. A controlled pressure is applied to the resin fills the voids. Then, the part is cured using a vacuum. However, the method can be improved by using an additional step. Aside from that, RTM can be a cost-effective method for complex three-dimensional shapes.
There are many variables and parameters that determine the quality of the process. The most significant parameters are the pressure, temperature, viscosity, and permeability of the resin. The RTM process also considers stratification and flow paths of the material. The flow dynamics of the resin depend on the fabric and thickness of the part. A single part that has high void content can be a problem. If the voids are a problem, the mould must be re-engineered.
The RTM mould has the advantages of being easy to clear. It also increases the production efficiency. Typically, it consists of a male mold and a female mold. A male mold is supplied with a main glue injection pipe and a glue extrusion pipe. In the final stages, the part is typically heat cured. After all these steps, an RTM mould is a great choice for a variety of applications.
The RTM process is the most effective and cost-effective method of injection moulding. The most important factor of an RTM mould is its quality. The mold is the key to the success of the process. It should be strong and reliable, with proper tooling. A bad mould can affect the performance of the product. In addition, it can cause serious problems. It is essential to choose the right one. It is also important to consider the size and shape of the part.
The RTM mould is typically made of metal and is often integrated with part ejectors and temperature control. The RTM mould can be designed to achieve the desired geometry. It is usually a one-shot process, but can also be divided into two-shot processes. This allows a manufacturer to manufacture complex geometries and shapes. The advantages of RTM injection moulds are many. The process is highly customized and you can choose the right mould for your needs.
A RTM mould is an essential part of the process. The materials used are matched with each other. The RTM process is a cost-efficient method for manufacturing complex objects. There are a few disadvantages of this moulding process. The initial investment is high. The RTM mould will require a lot of space. A mold should be big enough to contain the parts. It should also have a mould opening. There should be two inlet ports.
The RTM mould is a complex piece of equipment that allows a manufacturer to create a component using only a single piece. The RTM process can produce parts of any shape and size. The process requires a vacuum to create a cavity and the resin must be degassed before the mould can be filled. The RTM mould is usually equipped with a vacuum chamber. The resin must be degassed before it can be molded.