2023-09-01
PDCPD, or Polydicyclopentadiene, is a thermoset polymer that has gained significant attention for its remarkable properties. PDCPD Injection Molding Services leverage this material to produce a diverse range of products with exceptional durability, corrosion resistance, and impact strength. The process involves injecting molten PDCPD resin into a mold, where it cures and solidifies to form the desired shape. This method enables the creation of complex and intricate designs with precision and consistency.
Exceptional Durability: The Strength of PDCPD
One of the standout features of PDCPD Injection Molding Services is the exceptional durability that PDCPD resin imparts to the final products. PDCPD is known for its high impact resistance and ability to withstand harsh environmental conditions, including exposure to chemicals and UV radiation. This durability makes PDCPD-injected products well-suited for demanding applications where reliability and longevity are paramount, such as automotive parts, industrial enclosures, and utility infrastructure.
Design Flexibility: Crafting Complex Shapes
PDCPD Injection Molding Services excel in translating intricate designs into tangible products. The injection molding process allows for the creation of complex shapes, intricate detailing, and precise geometries that might be challenging to achieve with other manufacturing methods. This design flexibility opens doors to innovative product solutions, enabling manufacturers to push the boundaries of design and functionality.
Corrosion Resistance: Thriving in Challenging Environments
In industries where products are exposed to corrosive substances or extreme weather conditions, PDCPD Injection Molding Services offer a valuable solution. PDCPD resin naturally resists corrosion, making it an ideal choice for components used in environments with chemicals, saltwater, or other corrosive agents. This resistance ensures that products remain structurally sound and aesthetically pleasing even in challenging conditions.
Weight Reduction: Enhancing Efficiency
PDCPD's lightweight nature is a significant advantage in industries where weight reduction is a priority, such as automotive and aerospace. PDCPD Injection Molding Services enable the creation of lightweight yet strong components, contributing to overall efficiency and fuel economy. This weight reduction can have a cascading effect, impacting everything from vehicle performance to energy consumption.
Applications Across Industries: PDCPD's Versatility
The versatility of PDCPD Injection Molding Services is evident in their applications across various industries. In the automotive sector, PDCPD is used to create durable and lightweight body panels, bumpers, and interior components. In the industrial realm, it finds its place in enclosures, housings, and structural components that require a combination of strength and design flexibility. Additionally, the utility sector benefits from PDCPD-injected products for infrastructure elements like utility boxes and cable management systems.
Sustainability and Environmental Consciousness
As sustainability becomes a global priority, PDCPD Injection Molding Services align with environmentally conscious manufacturing practices. PDCPD resin is non-toxic and emits minimal volatile organic compounds (VOCs) during the molding process. Additionally, the durability and longevity of PDCPD-injected products contribute to reducing the need for frequent replacements, further minimizing environmental impact.
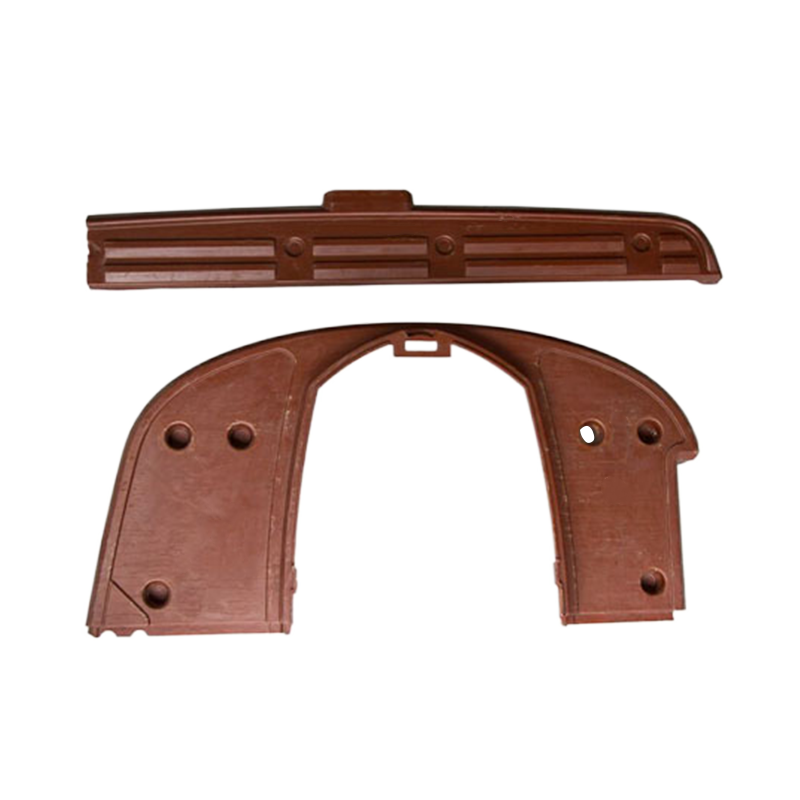