2023-09-01
The process of RTM involves the manual transfer of a polymer resin into an aluminum or steel mould. The tool is shaped to fit the product that is being moulded. It enables the injection of a specific amount of resin and can be manipulated by using a catalyst. During the process, a core or cavity is inserted into the mould. A tool is used to make the cavity or core. In addition, custom RTM moulds can have a very good surface finish. In addition to that, a gel coat can be introduced to improve the finish. The finished part can be painted or coated.
Using Custom RTM moulds can give you a competitive advantage in the marketplace. These tools are made of high-quality aluminum or steel and are capable of producing parts with a perfect finish. The RTM process is manual, and the tools are made of composite materials or aluminum. Moreover, a mould can be customized to meet the specific needs of the customer. If you're looking for a Custom RTM mould for your business, contact Taizhou Huangyan Shengfa Mould Co., Ltd.
The manufacturing process for Custom RTM moulds is a highly manual process that allows for varying amounts of reinforcing material and manipulated catalyst blend. A mould is manufactured using a core and cavity, which are made from aluminum or composite materials. The RTM process produces very good surface finishes. In some cases, gel coat is introduced to further improve the finish and provide a paint-ready surface. However, it is always best to contact an experienced manufacturer before ordering custom moulds.
Using Custom RTM moulds is a very cost-effective way to manufacture custom composite parts. It uses a manual process where the resin is injected into a closed mould. The process is very flexible and versatile, and you can use almost any material to create your products. When it comes to Custom RTM moulds, you can use any of these materials. You can choose to have a resin transfer mould made of titanium or other metal.
When designing custom RTM moulds, consider the material you'll be molding. Choosing the right material for your RTM moulds is critical. In addition to a high-quality composite part, RTM moulds also help manufacturers reduce costs. By choosing the right type of moulds, you can improve your production by saving time and money. You can even get your parts customized for a specific purpose with a custom mold.
Injection RTM moulds are essential for manufacturing high-quality composite parts. The process involves five main phases: the creation of a hollow part, a cavity, and an injection of resin. Once this is complete, a resin transfer mould will be created, resulting in a high-quality product. Once the mould has been created, the resin will be injected into the cavity. When the resin has cured, the part will be ready for painting.
RTM processes can be manual or automated. In addition to steel or aluminium moulds, Rotec uses aluminium or steel moulds. In an open mould, Rotec places layers of pre-cut fiberglass reinforcement. The size, shape, and weight of glass reinforcement are predetermined for each product. A closed mould is then clamped with a hydraulic press. A vacuum is applied to the closed mould, forcing the resin to flow through the cavity. The vacuum is then cured, and the finished product is ready to be painted.
The RTM process has five phases. The first phase is called the layup phase, and the second phase is the injection phase. The resin is injected into a closed mould. It is then cured by applying heat to the mould. The last phase is the final step in the manufacturing process: the final step. Once the mold has been made, the RTM process is completed. In the next phase, the product is poured into a new part.
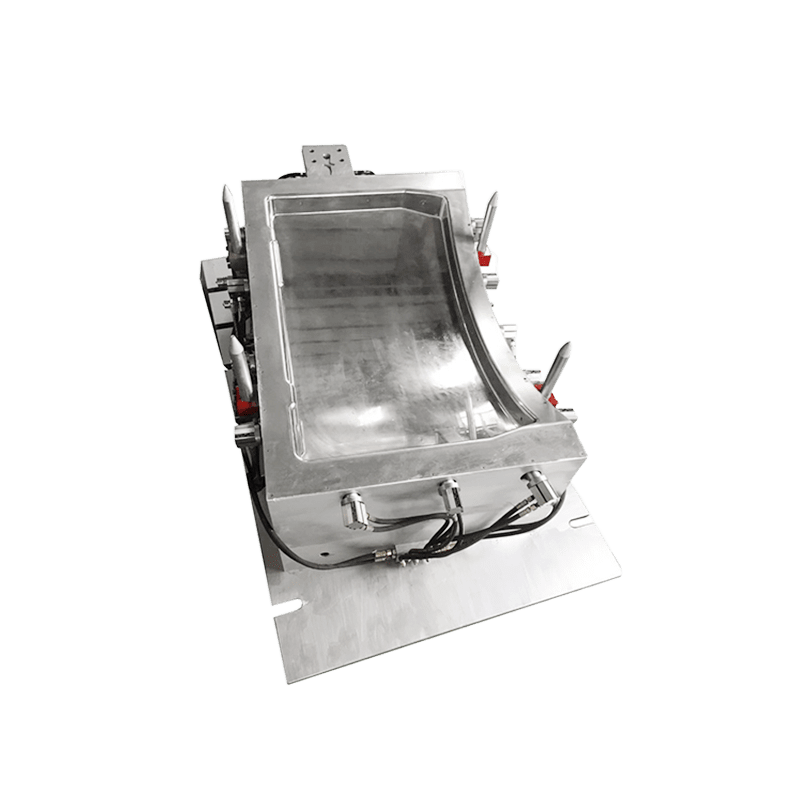