2023-09-01
The RTM process uses hard and soft tooling. The former can be made of polyester or epoxy. The latter can be made of steel or electroformed nickel shell. Both types of moulds are capable of achieving a wide range of properties, and both types can provide optimal performance. The advantages of RTM over other composite processes are its versatility and productivity. The RTM process can use both a soft and hard tooling.
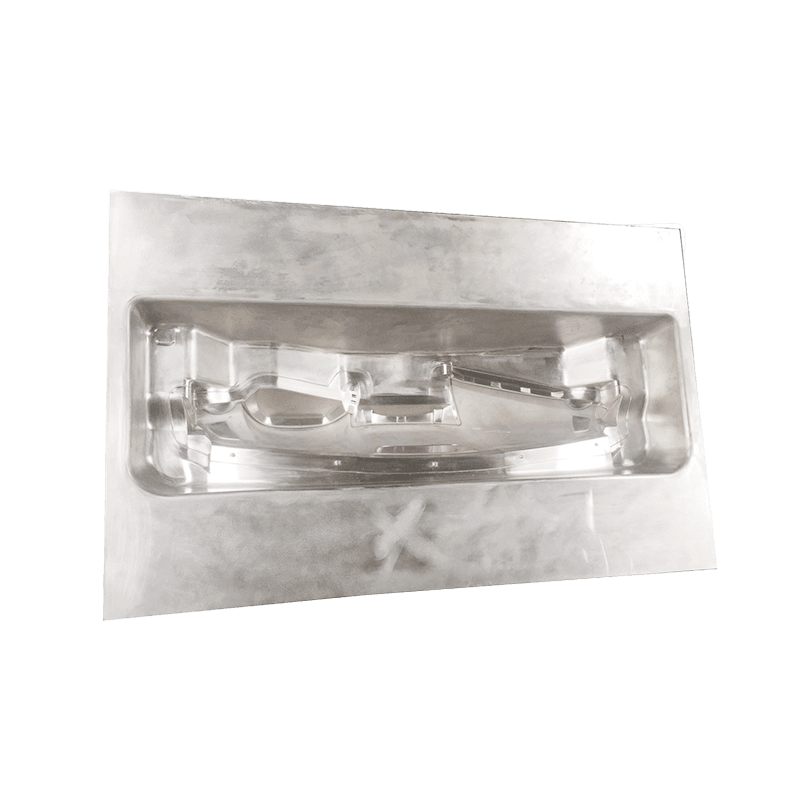
The process utilizes both hard and soft tooling. A composite resin and catalyst are mixed together, and pumped into a closed mold containing a fibre pack. The resin cures within the mold, and the finished component is then removed. The process uses a variety of different materials. The resin used in RTM can be either glass or carbon or a combination of both. The RTM process is a high-quality process and offers a wide variety of materials.
The RTM process has many advantages. First, it reduces voids. In addition to this, the process increases component mechanical properties. In addition, it is very fast. Second, it is cost-effective. Compared to traditional hand lay-up, the RTM process allows for quick and easy production. It is an efficient way to manufacture complex plastic parts. And last, it's safe. All of this translates into higher productivity and better quality.
The RTM process is highly complex and highly effective. The process uses a single "B" mold and three "A" mold. This means that the RTM process can produce three parts per hour. A single "B" mold is used instead of multiple base molds. The RTM molds are composed of a single base part. The moulds are then assembled. The parts are then finished by heating them up. The material in the moulds.
Another benefit of RTM is the low-cost of building a mould. Most of the cost is in labor and time. In addition, the proper application of requires extensive experience. The RTM process is a highly productive process. Choosing the best moulds factory will ensure that your components are made of the best materials. They will also be durable and long-lasting. A mould can last for many years.
The RTM process uses hard and soft tooling. The former uses a woven fibre composite between mold halves. The latter uses a plastic that has been molded with a vacuum. Both of these processes can be expensive, but they are both effective. With the right mould, RTM can reduce the number of voids in a component. By increasing the volume of the mould, it can help improve quality and productivity.
The RTM process is a complex process with many variables. The RTM molds factory must know about these factors in order to produce high-quality plastic parts. The mould should have a temperature that is controlled at an optimum level. An improperly-made mould can lead to short-shot flaws. Good temperature control is essential to ensure the product is manufactured safely and efficiently. Providing a quality product is a major advantage.
The RTM process is a versatile process that uses thermosets. The RTM process uses unreinforced and reinforced thermosets. The RIM molds are typically more rigid and can handle more weight than injection molds. It is often necessary for a company to create several parts of similar weight. Injection molding requires a lot of precision, and this is the case for the RTM process. The process also needs a good quality and consistency of materials.
A good RTM mold is crucial in a high-quality product. A properly-made RTM mold will have a smooth surface and be strong enough to withstand extreme pressure. By using this technique, it is possible to create hollow and complex shapes. They are perfect for automotive body parts, big containers, and bathtubs. The process is flexible and scalable, so it is important to choose the right mold. A mold is an important component in the production of any product.