2023-09-01
The PDCPD molding process involves injecting a liquid resin into a mold, which is then heated and cured to form a solid component. The mold can be made of various materials such as aluminum, steel, or composite materials. The PDCPD material is highly versatile, which makes it possible to mold complex shapes with precision and accuracy. Moreover, PDCPD is highly resistant to corrosion, UV radiation, and impact, making it ideal for automotive components that are exposed to harsh environmental conditions.
One of the main applications of PDCPD in the automotive industry is in the production of exterior body panels. These panels require high strength, durability, and resistance to impact and weathering. PDCPD meets all of these requirements, making it an ideal material for use in fenders, hoods, roofs, and other exterior components. PDCPD also provides excellent dimensional stability, which is essential for ensuring consistent fit and finish.
Another area where PDCPD is widely used in the automotive industry is in the production of structural components such as brackets, frames, and supports. These components require high strength and stiffness, and PDCPD provides both of these properties while also being lightweight. PDCPD can also be molded with reinforcing fibers such as glass or carbon, which further enhances its strength and stiffness.
In addition to exterior body panels and structural components, PDCPD is also used in the automotive industry for interior components such as instrument panels, door panels, and seating. PDCPD offers excellent surface finish and can be molded with various textures and colors, making it an ideal material for use in high-end automotive interiors.
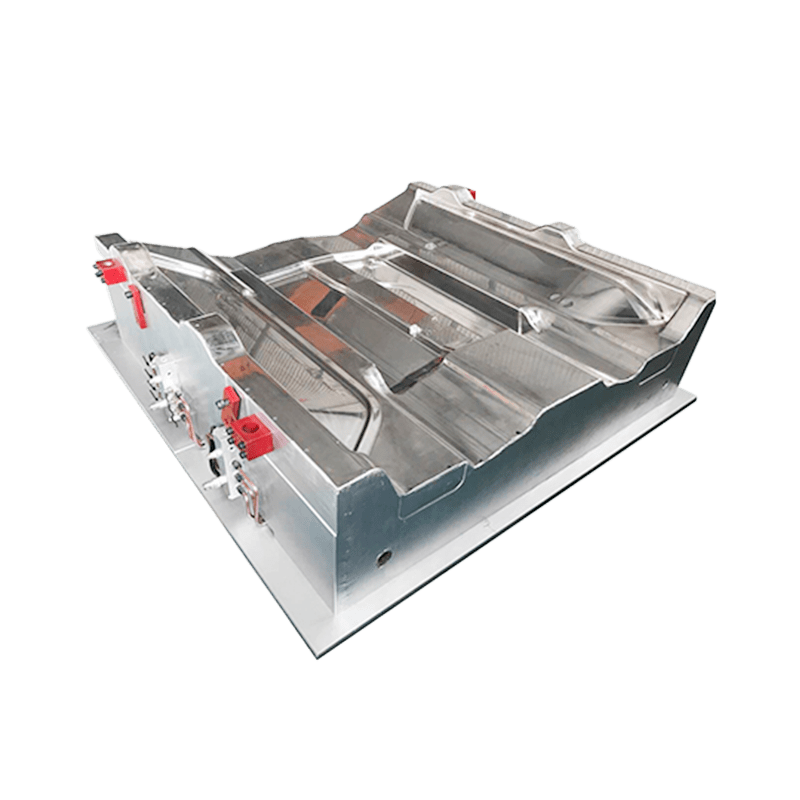