2023-09-01
RTM molds allow for the creation of complex geometries and intricate designs that would be challenging or impossible to achieve using traditional manufacturing methods. The molds can be precisely engineered to replicate intricate shapes and details, enabling manufacturers to produce parts with superior aesthetics and functionality. This design freedom broadens the possibilities for product innovation and differentiation in industries such as aerospace, automotive, and wind energy.
2. Consistent and Reproducible Quality:
One of the key advantages of RTM molds is their ability to deliver consistent and reproducible part quality. The closed-mold process ensures controlled resin flow, minimizing variations and defects in the final composite component. Manufacturers can achieve tight tolerances, excellent surface finish, and consistent mechanical properties across production runs, ensuring reliable and high-performance products.
3. Enhanced Strength-to-Weight Ratio:
RTM molds enable the production of composite parts with an exceptional strength-to-weight ratio. By precisely controlling the resin infusion process, the molds allow for the placement of reinforcement materials in optimal positions, maximizing the structural performance of the final component. This results in lightweight yet robust parts that offer superior strength and durability compared to traditional materials.
4. Reduced Material Waste:
The closed-mold nature of RTM molds minimizes material waste during the manufacturing process. Resin is injected into a precisely defined cavity, ensuring that the exact amount of resin required for the component is used. This efficiency helps reduce material costs and contributes to sustainable manufacturing practices by minimizing waste generation.
5. Faster Production Cycle:
RTM molds offer faster production cycles compared to other composite manufacturing methods. The precise control of resin flow and curing times enables accelerated production processes. The molds allow for shorter infusion and curing times, leading to increased production rates and improved overall manufacturing efficiency. This is particularly beneficial in industries with high demand and time-sensitive production schedules.
6. Scalability and Cost-Effectiveness:
RTM molds are scalable and suitable for both small-scale and large-scale production. The ability to replicate complex parts consistently and efficiently makes RTM an attractive option for manufacturers looking to produce components in various quantities. Additionally, the closed-mold process reduces labor-intensive tasks, such as hand lay-up or vacuum bagging, resulting in cost savings and increased productivity.
7. Improved Worker Safety:
RTM molds contribute to enhanced worker safety compared to traditional composite manufacturing methods. The closed-mold process minimizes exposure to harmful chemicals and reduces the risk of worker contact with resin, resulting in a safer working environment. The use of automated or semi-automated RTM systems further reduces manual labor and associated safety hazards.
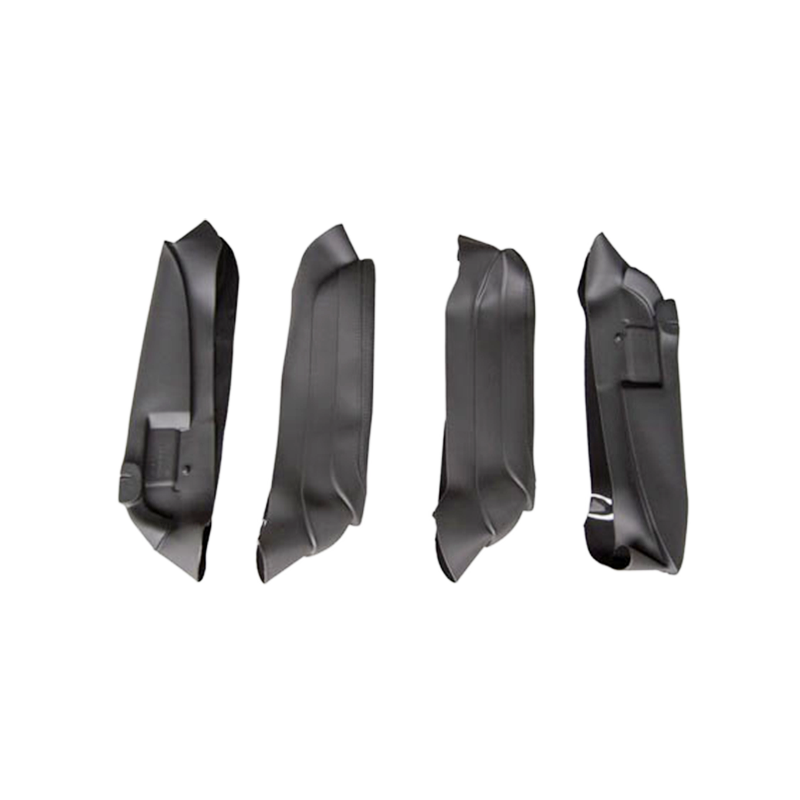