2023-09-01
The manufacturing process of RTM moulds consists of five stages, namely the design, moulding, product injection, and curing. The process starts by placing a dry fiber preform into a metal mold. This closed mould compactions the preform to a specified volume fraction. After this, a liquid thermosetting resin is injected into the mould. This is usually done at a very high pressure. In order to avoid problems, both the mold and the resin are heated before and after the injection. These processes can also be performed under vacuum, which helps to remove any trapped air.
The injection pressure determines the amount of resin that is injected into the mold. It also determines how much resin will flow into the mould, which affects its hydraulic pressure. This process also involves controlling the injection time. It must be long enough so that the product does not gel prematurely. The temperature of the injection fluid is also an important parameter.
The design process of RTM moulds also involves the preform selection and the preform geometry. Using the appropriate preform will enable the mould to achieve high-quality composite parts. By creating a mould with a preform, the manufacturing process becomes simpler and quicker. The use of preform technology also helps build complex net-shaped 3D structures.
Another important aspect of RTM moulds is their pressure controls. A pressure sensor is installed in the channel that distributes the resin through the mould. This is important to ensure the process is smooth and accurate. It is also important to remember that pressure inside the mold does not match the pressure inside the mold. Therefore, the operator must be aware of the internal pressure in order to ensure that the resin is always filled and that the resin is not too hot or cold.
Custom RTM moulds can help companies manufacture a range of plastic parts. These moulds are made to suit specific product shapes, weights, and sizes. A custom RTM mould can produce an excellent surface finish and can be coated with gel coat or paint. These moulds are usually made of high-quality aluminum or steel.
Another important aspect of RTM moulds is their durability. The traditional RTM moulds were very heavy, and required heavy lifting machinery to handle them. Today, most plants handle RTM moulds up to 10 square meters. However, if the moulds are very large, they might require an elevator. Electric industrial lifting systems can handle moulds with up to 220 kg, and are becoming more common in industry.
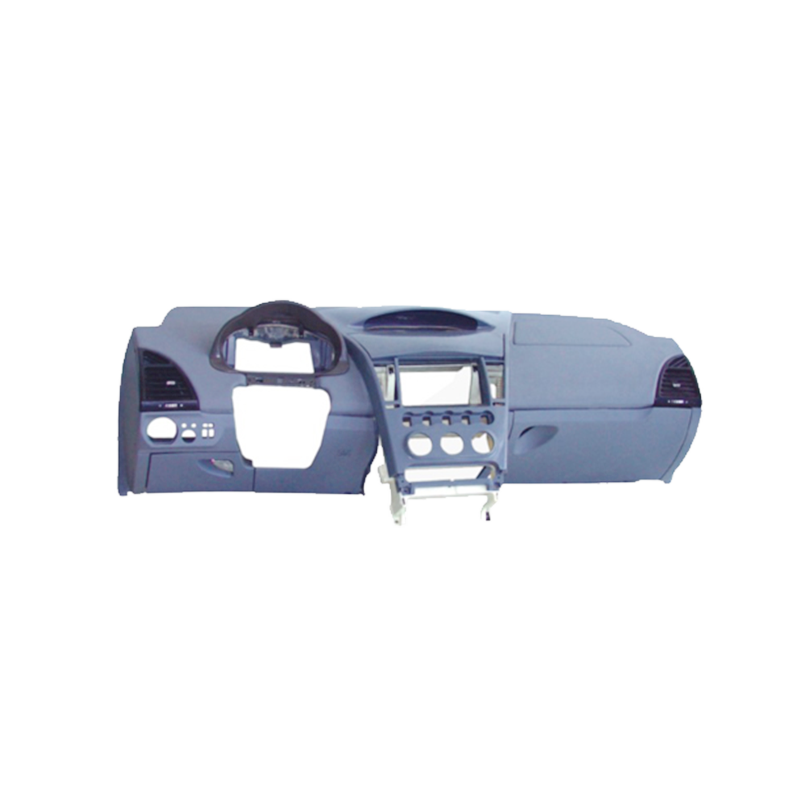