2023-09-01
Slush molding is a low-cost process that produces hollow plastic components. It involves pouring molten polymer into a mold and letting it cool for a short period. Then, the mold is split, releasing the excess polymer and forming a hollow component. This process can be used to manufacture a variety of hollow components and is much cheaper than manufacturing solid components.
Slush molding is an environmentally-friendly process that provides enhanced features over incumbent products. It can be used to manufacture soft-touch interior applications and can be run in existing slush processes. It can save up to 30 percent in weight due to its thin-walled construction. Another advantage of this process is that it does not require additional tooling.
Another benefit of slush mold casting is its ability to produce hollow castings. It can produce a range of materials, from plastics and foams to metals and other alloys. Slush molds are especially beneficial for casting parts with low melting points, such as zinc, tin, and aluminum alloys.
The mold is then inverted. Its cavity is then removed, and the inverted mold is transported by conveyor 10 to station II. A chain conveyor then returns the empty mold to Station I. A chain conveyor then removes the mold from the filling station and returns it to the filling station. The mold is then ready to be reused.
After the mold is refilled, it is rotated while it fuses the plastisol-based coating. This allows the air bubbles to expand and form a smoother skin. The process is also beneficial in that it allows for removal of excess plastisol from the mold while rotating. It also allows for a more even distribution of heat and minimizes the risk of localized scorching. The total thickness of the coating 28 is between 40 and 80 mils.
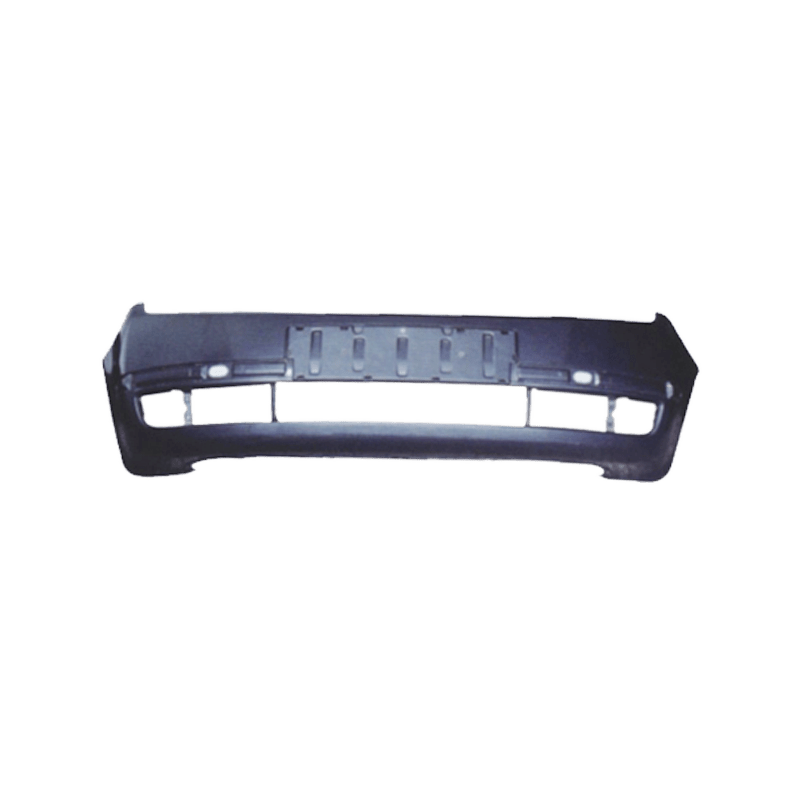