2023-09-01
The RTM process starts with a gel-coated mold. This process ensures a high quality finish. The next step is to add reinforcements or other materials. Once the resin has been injected, the resin is then cured. Finally, the mold is heated to ensure that the rigid part remains in place. As mentioned, the tooling used in the RTM process can be hard or soft. In general, a soft mold will be made from polyester, epoxy, or some other plastic. A hard mold would be made from a machined aluminium/steel shell or from an electroformed nickel shell.
The temperature of the RTM mould is crucial for the process. The injection pressure is important for the holding force of the mould. Likewise, the resin viscosity is important for the flow of the resin within the mold. This will prevent premature gelation of the resin. Therefore, the design of an RTM mould is crucial to the successful production of FRP components. Once the process is complete, the parts are sent to the finishing department for assembly.
The main benefit of RTM molds is the high quality of finished parts. Since the mold determines the geometry of the part, it dictates how the resin will flow. It also supplies heat to polymerize the material. Once the process is complete, the part remains rigid within the mold. For this reason, RTM Molds are an essential element of the process. If your part requires precise tolerances, you need a mold that is designed for that exact type of plastic.
Another benefit of RTM Molds is their ease of use. These machines are used to produce complex and large-scale parts. The process can be very complicated if the materials are too soft. Fortunately, it doesn't require any special tools. It just needs a pair of female and male molds. And the process is quick, resulting in the high quality part you're looking for. It is a great way to build a new product from a unique design.
RTM is a good choice for long-bladed wind turbines. This type of material can be used for a variety of applications. From wind turbine blades to boat hulls, RTM can be used to make airplane parts. The process is fast and easy to use, and the quality of the parts is high, too. It is perfect for high-quality, long-bladed wind turbines. They are the best for a variety of reasons.
RTM Molds can be used in many different ways. Some types of molds are soft, while others are hard. Those that are made of a soft material are more easily moldable, while those with a hard material are more resistant to chemicals. They can also be more durable and last longer than other materials. Some RTM moulds are even reusable, which means that they will last for several years. However, they may not have the same durability as a plastic mold, and they can be more difficult to handle.
A RTM mold is a closed moulding process. It is a very efficient method of making large-volume, high-performance composite parts. A low-volume mold is a good choice for smaller production quantities. There are two main types of RTM Molds: those that are made of plastic, and those that are made of steel. If you want to know more about the benefits of both, read on. The advantages of each type are listed below.
Injection pressure in an RTM mold is very high and is critical for a successful FRP component. The temperature and viscosity of the resin are the two other variables that affect the flow of the resin. The injection pressure is also a critical factor, as it controls the amount of resin. It should be high enough to ensure that the resin is properly cured. The pressure of the injection is regulated to prevent air entrapment.
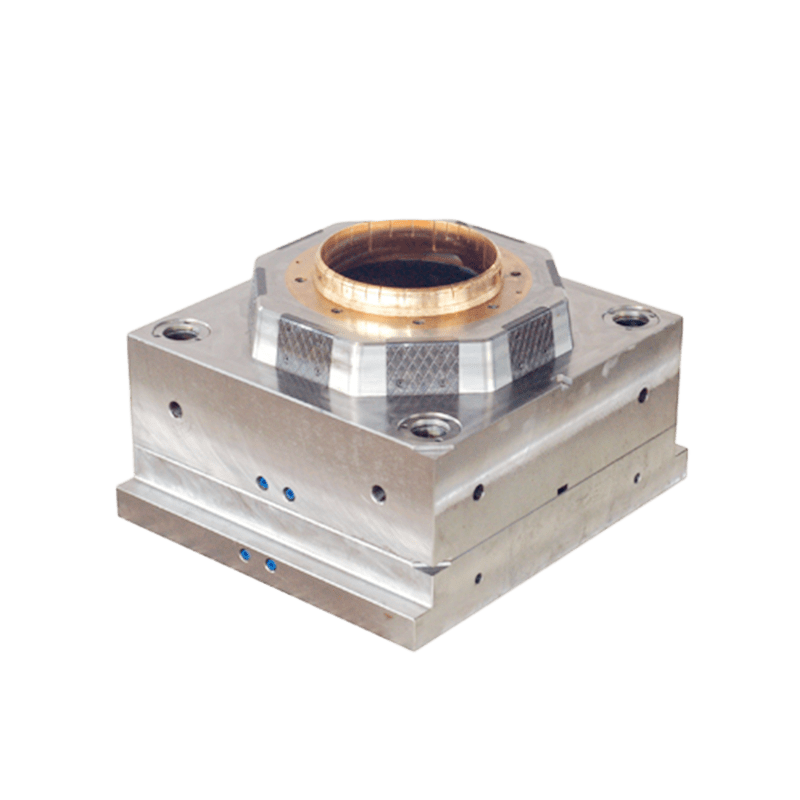