2023-09-01
Typically, the injection pressure is four to 10 bars, depending on the complexity of the part. The uncured liquid resin is then injected into the mold cavity, filling the space between the layers of fibers. The process displaces the entrapped air through air vents within the mold. Afterward, the resin-catalyst system is dried at room temperature or elevated in an air-circulating oven. Once cured, the parts may need trimming to obtain final dimensions.
RTM Molds are available with either a heated or room-temperature design. The temperature of the mould and the pressure of the resin injection are all key process parameters for successful RTM. The mould's configuration and the viscosity of the resin are critical factors for success. Improperly designed RTM molds may cause deformation of the fibre preform. High temperatures can lead to short-shot flaws and increased production costs. The right temperature control is essential to ensure the smoothest and most consistent parts.
The process of RTM begins with the injection of a dry fiber reinforcement into a mold cavity. After this, the resin is injected under pressure into the mold cavity. After the injection, the resin is allowed to cure at room temperature or elevated temperature. The cured part may require trimming to reach the final dimensions. It is important to check that the RTM molds are properly insulated. You need to keep them cool enough to prevent overheating.
For fast cycle times and consistent product quality, heated RTM molds are essential for a smooth, quality end-product. When the resin has reached the desired temperature, the part will be molded. This process is also known as extrusion. The process of RTM molding involves three steps. First, the material used in the resin is melted in the mold. Once this is completed, the mould is removed and the resin is cured in the mould.
The RTM process is a highly flexible process. The RTM molding process starts with the gel coating of the mold, which guarantees a high-quality end product. Then, the resin is injected under pressure and cured in the mold. After the resin has cured in the mold, the part is finished on both sides. It can be used for a wide variety of products, including automotive and aerospace industries. The RTM technique can be a cost-effective way to produce a high-quality, durable product.
The RTM process is an integral part of a wind turbine blade. The process requires a mold with a core, cavity, and counter mold. Once the core has been molded, the reinforced material is loaded into the mold. Then, the mold is closed and heated, which preserves the rigidity of the finished product. Once the resin is in the cavity, the entire process is complete. However, the resin is not the only material that will be injected into a wind turbine.
The RTM process is a low-pressure molding process. The resin is injected into a mold with a fibre pack and then cured inside the mould. The finished component can be opened to be removed. This process is highly versatile and can produce a variety of components. Unlike traditional processes, RTM moulds can be made of glass, carbon, arimid, or a combination of fibres. When the resin is injected in a mold, the resin is cured within the mold.
The RTM process begins with a gel coating on the mold, which produces a high-quality finished product. After this, the mold is filled with the required material. A high-pressure resin is injected into the mold under pressure. Then the mold is closed and heated, which maintains the rigidity of the part. The tooling used in the RTM process can be soft or hard. A polyester or epoxy mould is a soft tooling, while a hard aluminum/steel or nickel shell is a hard tooling.
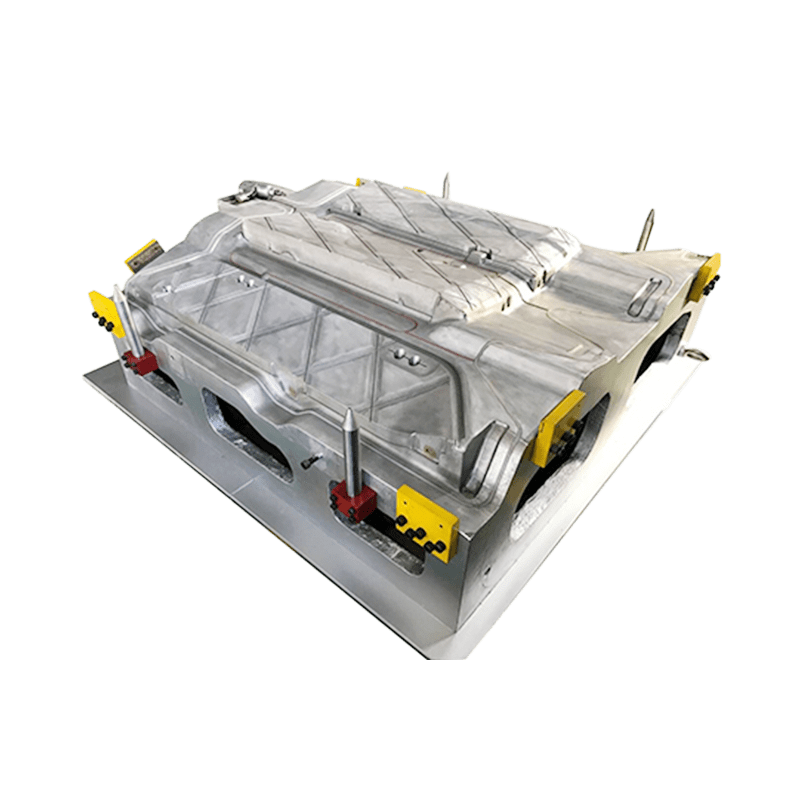