2023-09-01
2. Design Flexibility: PDCPD molds offer design flexibility, enabling the production of components with complex geometries and integrated features. The low viscosity of the PDCPD material allows for easy flow and fills intricate mold cavities, resulting in parts with excellent detail reproduction. Moreover, PDCPD molds can incorporate inserts, reinforcement fibers, or metal inserts to enhance specific properties or functionality. The design flexibility of PDCPD molds allows for the creation of lightweight and structurally robust components.
3. Production Efficiency: PDCPD molds contribute to production efficiency due to their fast curing time and short cycle times. PDCPD materials have rapid curing characteristics, enabling faster demolding and reducing overall production time. The low viscosity of the material facilitates easy flow and complete mold filling, leading to shorter injection and cure cycles. This efficiency advantage makes PDCPD molds suitable for high-volume production and helps reduce manufacturing costs.
4. Mold Construction and Surface Finish: The construction and surface finish of PDCPD molds are crucial considerations. PDCPD molds are typically made from materials such as aluminum or epoxy, which offer good thermal conductivity, dimensional stability, and surface smoothness. These characteristics allow for efficient heat transfer during the curing process and ensure excellent surface quality in the final components. The mold surface should be properly treated or coated to provide easy part release and enhance the aesthetics of the molded parts.
5. Material Compatibility: When utilizing PDCPD molds, it is important to consider material compatibility. PDCPD resins are available in various grades with different properties, including impact strength, heat resistance, or electrical conductivity. Understanding the specific material requirements of the intended application and selecting the appropriate PDCPD resin is essential to achieve optimal performance and meet industry standards.
6. Mold Venting and Gating: Proper mold venting and gating are critical for successful PDCPD mold processes. Venting allows for the controlled release of air and volatiles during resin injection, preventing the formation of air traps or voids in the molded parts. Efficient gating systems ensure uniform resin flow and filling of the mold cavities, minimizing the risk of defects. Proper mold venting and gating contribute to the production of high-quality PDCPD components with consistent properties.
7. Mold Maintenance and Serviceability: Proper maintenance and serviceability of PDCPD molds are important for their longevity and optimal performance. Regular cleaning, inspection, and lubrication of the mold components help prevent defects, improve efficiency, and extend the mold's lifespan. Additionally, ensuring access to reliable mold maintenance services and technical support from the mold manufacturer or supplier is crucial for troubleshooting and resolving any issues that may arise during production.
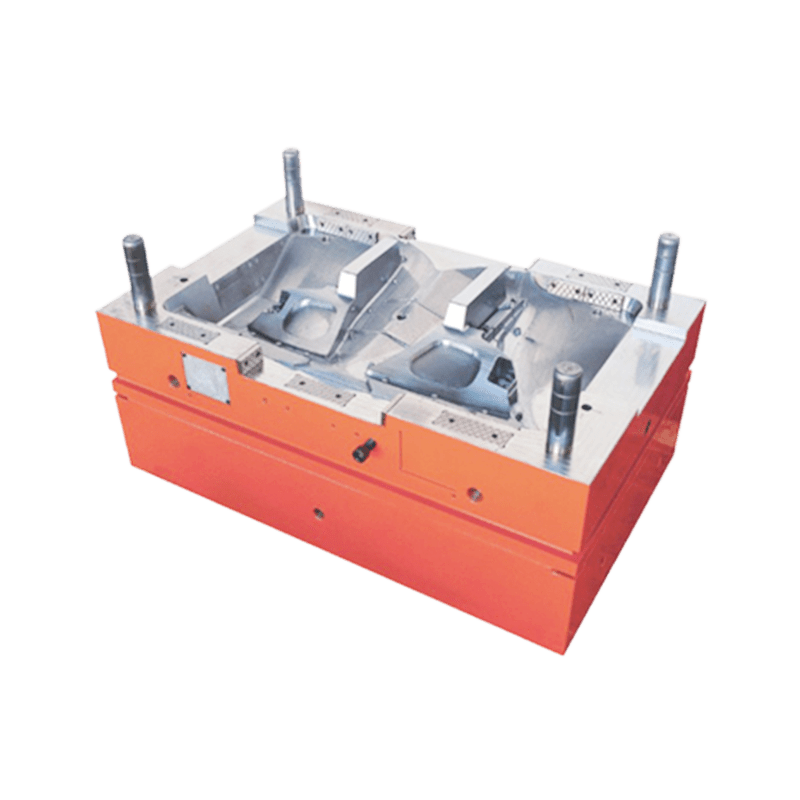