2023-09-01
2. Cost-Effectiveness: RTM molds offer cost-effective manufacturing solutions for composite parts. The closed mold system reduces material waste and allows for the efficient use of resin, reinforcing fibers, and core materials. Additionally, the ability to produce complex shapes and integrate multiple components into a single mold helps streamline the production process, reducing assembly and labor costs. The cost-effectiveness of RTM molds makes them suitable for both small-scale and large-scale production.
3. Design Flexibility: RTM molds provide significant design flexibility, allowing the production of parts with intricate geometries, varying thicknesses, and integrated features. The molds can be designed to accommodate inserts, cores, or additional components, enabling the creation of complex composite structures in a single manufacturing step. This design freedom makes RTM molds suitable for a wide range of industries, including automotive, aerospace, marine, and consumer goods.
4. Material Selection: The choice of materials is a critical consideration when utilizing RTM molds. The molds should be compatible with the specific resin system and reinforcing fibers being used. Common resin systems include polyester, epoxy, vinyl ester, and polyurethane, each with its own mechanical, thermal, and chemical properties. Similarly, various types of reinforcing fibers, such as fiberglass, carbon fiber, or aramid, offer different strength-to-weight ratios and stiffness characteristics. Understanding the material compatibility and selecting suitable combinations is vital to achieve the desired performance and properties in the final composite parts.
5. Mold Venting and Permeability: Proper mold venting and permeability are essential considerations in the RTM mold process. Venting allows for the controlled release of air and volatiles during resin injection, preventing the formation of trapped air pockets or resin voids in the part. Mold permeability refers to the ability of the mold material to allow resin flow through the mold cavity. Optimal venting and permeability ensure uniform resin distribution, minimize the risk of defects, and enhance the mechanical properties of the final parts.
6. Mold Release and Surface Treatment: Adequate mold release and surface treatment are important factors to consider when using RTM molds. The mold surfaces should be treated with appropriate release agents to prevent adhesion of the resin to the mold, facilitating easy part demolding. Surface treatment techniques, such as polishing or applying surface coatings, can enhance the surface finish of the final parts. Proper mold release and surface treatment ensure smooth demolding and improve the aesthetics of the composite parts.
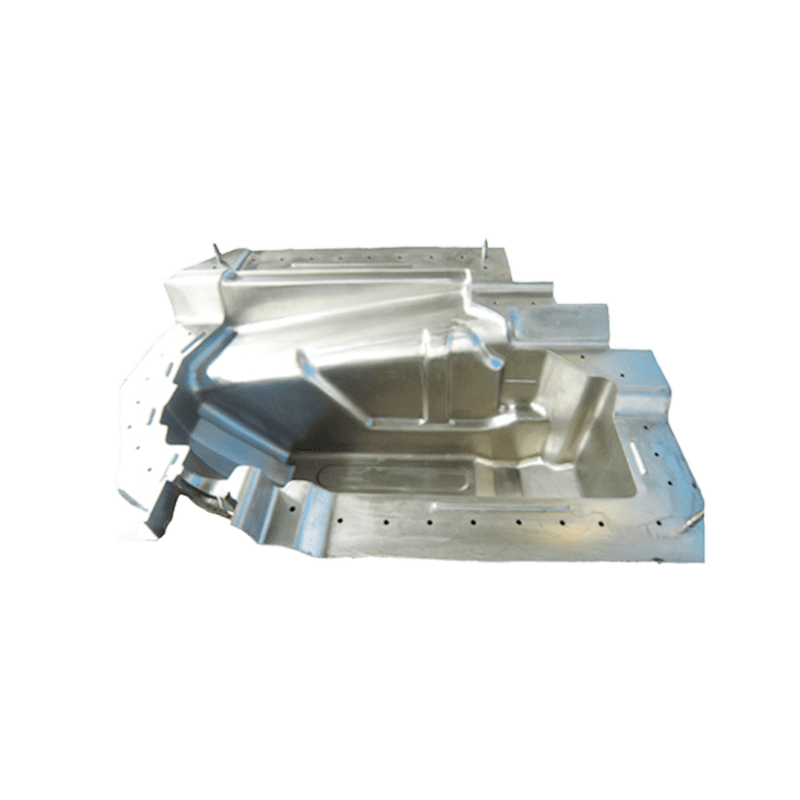