2023-09-01
This process is manual and involves heavy investments in moulds, injection equipment and tools, and is suitable for many industries. The process is environmentally friendly, requiring low amounts of consumables and limiting solvent emissions within the production workshop. Because of its versatility and high-quality finish, RTM has become the preferred method of manufacture for parts that need excellent surface finishes and a consistent thickness. In many fields, the process has become the norm, and it is part of a wider movement towards sustainable manufacturing.
Custom RTM Moulds are important for producing high-quality resin-filled products. These moulds should be designed to suit your specific requirements, and should be produced in a number of pieces. The process is more advanced than ever, and it is becoming a more popular fabrication method. It is possible to find a mould that is specifically designed for your application. If you want to learn more about this technology, take a look at the following:
Custom RTM Moulds are essential to a successful RTM process. This method requires significant investments in the right moulds and injection equipment, as well as inexperience. While it has a high level of precision, it is also a highly complex process that requires know-how and expertise. As the popularity of RTM grows in the manufacturing sector, it is increasingly becoming the preferred choice for many industries. It is replacing spray up technologies and contact moulding.
The process is complex and requires a significant investment in moulds and injection equipment. A specialized process called Vacuum Assisted Resin Transfer Molding uses a vacuum to assist the process. The vacuum helps the resin flow into the mould, and the heat helps the resin cure. In addition to creating a durable composite product, RTM also makes it possible to incorporate metallic inserts, foam, and other components.
The process is highly manual and involves a high-precision resin injection. The process can also be automated and utilize a vacuum. Depending on the application, custom RTM moulds are often used to produce high-performance composite components. Using these moulds, we can also create a variety of products that are not only customized but also customized. There are many advantages to custom moulds. The process can be automated.
The RTM process is a complex process that involves the injection of liquid resin into a metal mould. Using steel or aluminium moulds, Rotec inserts layers of pre-cut fiberglass reinforcement into the open mould. The layers are precisely predetermined for each product. Afterward, a hydraulic press clamps the closed mould. After the glass reinforcement is placed into the closed mould, the resin is injected into the mold and cured.
The process of RTM uses closed moulds and uses a low pressure to force the resin into the mould. However, the process is not limited to these types of molds. It can also use an external vacuum to aid the process. This vacuum is a necessary tool in many cases. Infusion moulds use an inner mold that requires a high-pressure resin injection. A Vacuum-assisted RTM mould is a great solution for several applications.
Typically, an RTM mould is made of aluminium or steel. The two types of moulds are very similar, and the size and shape of the parts are the only differences. The process requires a core, a cavity, and tools. Aluminum or composite materials are common for these moulds. It is a highly-controlled process that can produce parts of very high quality with excellent surface finishes. In addition to this, RTM moulds are also very affordable.
During the RTM process, moulds are made of aluminium or steel. After a dry fibre preform is inserted into an open mould, the resin is pumped into the mould cavity and cured by applying hydrostatic pressure. The process has several advantages. It can produce composite parts with excellent dimensional control. Moreover, RTM moulds can be used for co-curing foam, metallic inserts, and pre-cured details.
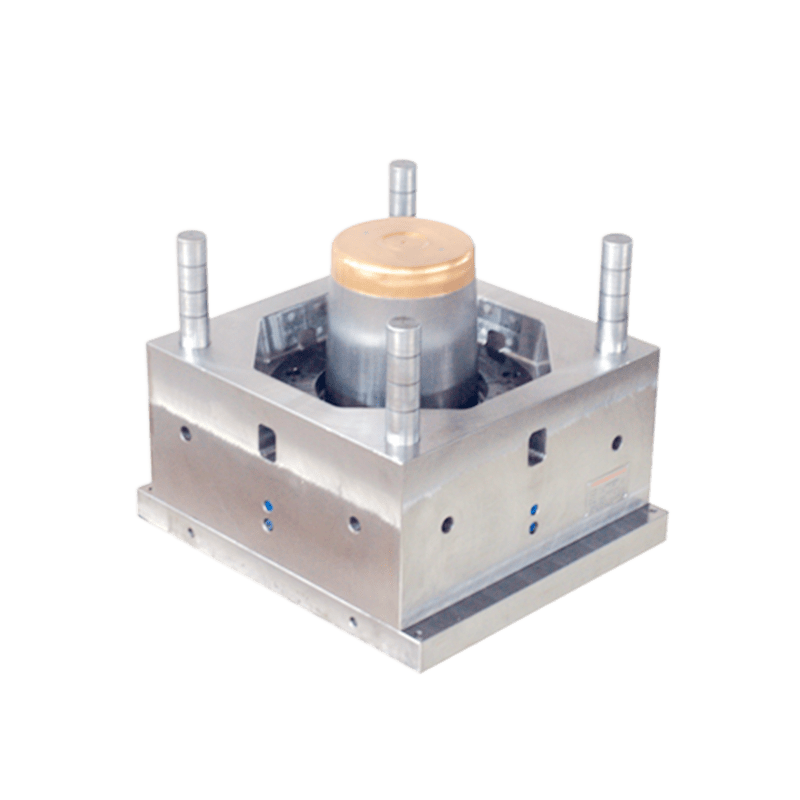