2023-09-01
The design advantages of PDCPD are numerous. For example, a RIM tool can be used to insert molded-in inserts in any part, even if the transitions between the different materials are severe. Another benefit is that a low-pressure RIM process allows the molded-in stresses to be kept to a minimum. The process is also fast, with a cycle time ranging from four to six minutes.
While RIM has been used for decades for its RIM component, the polymer is only now being used for heavy-duty applications. The new material offers several advantages over traditional materials, such as fiberglass, aluminum, and polyester. Its lower cost and fewer processing requirements make it an attractive alternative to these conventional materials. There are a variety of uses for P-DCPD. Listed below are some of its key advantages.
P-DCPD is the ideal material for many heavy-duty applications. It is highly flexible and durable and has a lower specific gravity than FRP, making it more suitable for industrial use. This polymer is also resistant to impact and is therefore a better choice for a variety of industrial applications. The low viscosity of P-DCPD makes it an ideal material for the RIM process. This makes the material highly desirable in heavy-duty trucks.
P-DCPD has many advantages. It is a flexible thermoplastic that offers greater flexibility than FRP. This makes it an excellent choice for applications that require high flexibility, such as structural parts. Moreover, it is also less flammable and reduces the need for expensive steel. As a result, P-DCPD is an excellent choice for a wide variety of industrial applications. Its properties make it an efficient choice for the RIM process.
While RIM is a relatively simple process, the RIM process is extremely efficient. It is used in less than ten percent of heavy trucks. Its low viscosity makes it easy to form. It is also highly flexible. This makes it a popular material for many industrial applications. However, it is not yet widely used. Its low viscosity can cause problems during the process. It is a disadvantage of RIM.
While it is a good material for structural applications, P-DCPD is also a good choice for other industrial applications. It has a high tensile strength and low flexural modulus, making it an excellent material for vehicles and other components. It also offers low-pressure pouring and is easy to mold without knit lines. This makes it a highly versatile material. The process is also very efficient. Ultimately, it will save you money.
The PDCPD process is the most popular material for P-DCPD. It is used in RIM systems in a low-pressure (15-30 kPa). It is a good choice for a variety of industrial applications due to its low specific gravity and low viscosity. In addition, the RIM process is very efficient. It also produces parts of higher quality. The advantages of the Rim are similar to those of urethane.
Its low specific gravity and low viscosity makes it a good material for a number of industrial applications. Compared to urethane, it is less expensive to produce than urethane and has lower processing requirements. Further, its low viscosity allows it to be molded directly into holes without knit lines. This is an important advantage of the Rim PDCPD system. There are many advantages of this system.
The P-DCPD RIM is a lightweight material and offers significant benefits. The compound is less viscous than SMC and has a lower tensile modulus. Its low specific gravity makes it an excellent choice for a variety of industrial applications. The low viscosity also makes it ideal for large-scale parts weighing between 20 and 150 pounds. This resin is also highly flammable and can be used in a range of different conditions.
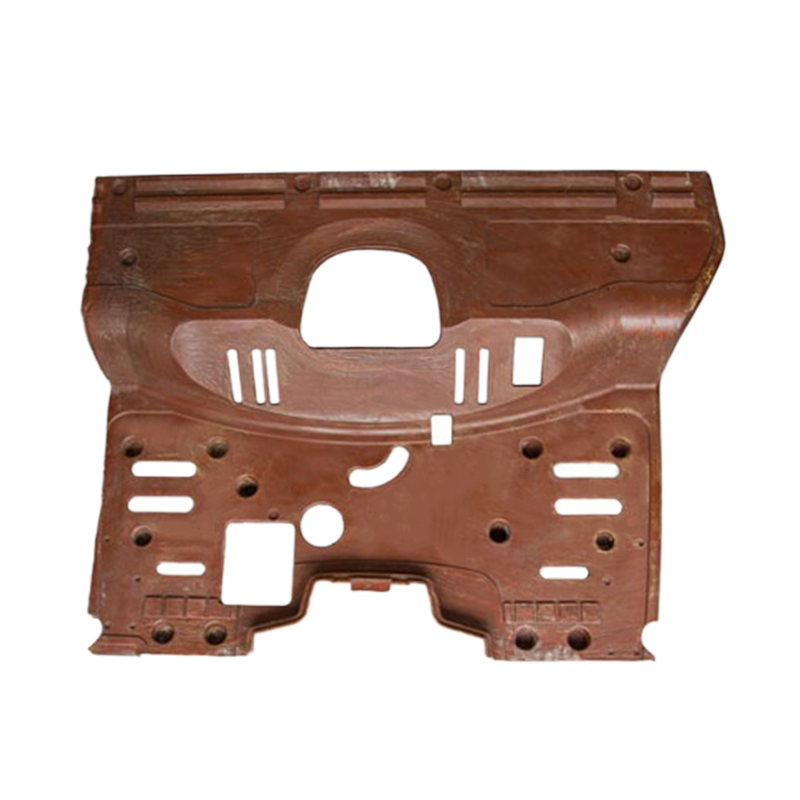