2023-09-01
The resin transfer moulding process is manual, but can be done with a high-quality composite resin. The RTM process is suitable for almost any reinforcing material. The catalyst blend can be controlled or modified, and the mould is closed. The resin is then pumped into the tool cavity. The finished part can then be opened and inspected to determine the quality of the part. If necessary, the mould can be closed for removal.
The process of custom resin transfer molding requires a substantial investment in moulds and injection equipment, such as hydrostatic presses for high-pressure injection. It is not a cheap process, though. A well-designed RTM process requires an experienced partner with extensive knowledge and experience. The RTM process has been taking over spray up technologies and contact moulding, and it is becoming the norm in many fields of activity. There are many benefits to the RTM process and it's time to get your company on the right track with it.
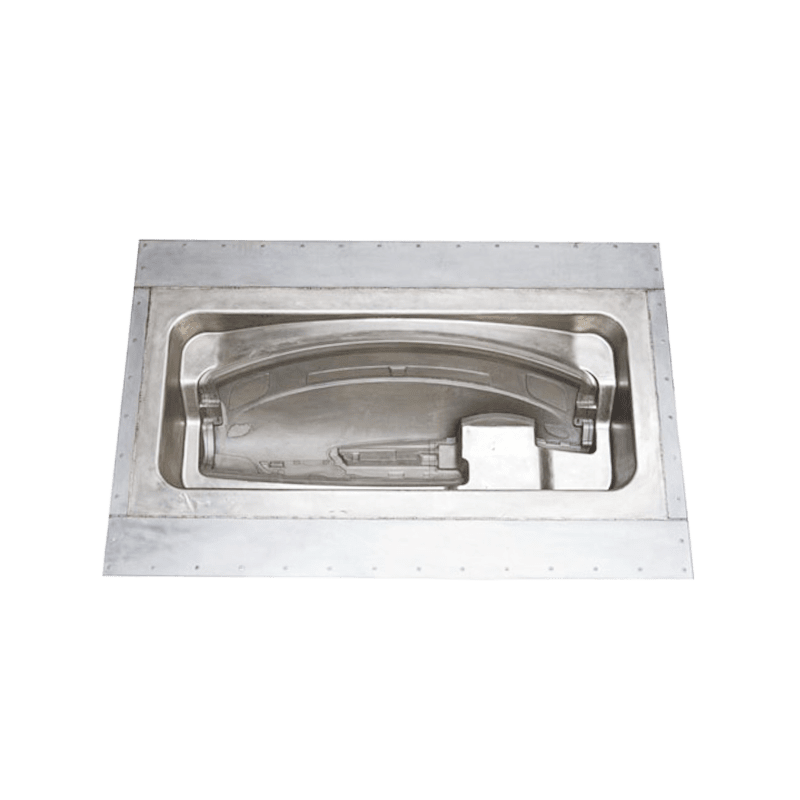
Custom RTM Moulds allow your company to get the exact parts you need. With the right RTM Mould, you'll see a higher quality end-product and less time spent on mould design. You'll be able to design your own moulds and have the flexibility to experiment with various combinations of materials. You'll be able to manufacture high-quality products and save a lot of money in the process.
Custom RTM Moulds offer a high level of flexibility and versatility. You can incorporate almost any reinforcement and catalyst blend you need. You will need a core and a cavity. You will also need tools to make the RTM process. Some of these tools are made from composite materials, while others are made of aluminum. The quality of the resin transfer moulded part depends on the tool used. If the parts need to be molded into a complex product, it may be better to use a custom mold.
There are many advantages to RTM. Infusion moulds require less expensive materials and are more environmentally friendly. Because of its flexibility, RTM is a great option for companies that need to make large-scale parts. With a custom RTM Mould, you can choose between a wide range of materials, including aluminum and composite. You can also choose to add a gel coat for better surface finishes. This type of moulding makes a resin-based part very durable and paint-ready.
Custom RTM Moulds are ideal for high-volume production. It is easy to customize a custom RTM mould. The process of resin transfer molding involves inserting a preform into a metal mould and injecting a liquid resin into the cavity. The process uses hydrostatic pressure to consolidate the preform, and the resulting parts have excellent dimensional control. Furthermore, RTM processes can also include metallic inserts and pre-cured details.
Resin transfer moulding is a closed-moulding process, which involves the injection of a mixture of resin and reinforcement materials into a mould. This process is a manual process, requiring a cavity and core. To produce a custom RTM part, you need a solid-reinforced, insulated resin. These components are usually made of a composite or aluminum resin.
The resin transfer moulding process is a closed moulding technique that produces high-performance composite components. The tools used in this process are made of metal tools that fit together. Dry fibre preforms are inserted into the mould cavity, and resin is then injected through the tool. After the resin is injected, the tool is closed and the part is then removed. A good quality mould is an important factor in an efficient manufacturing process.
The process begins with an open mould with layers of fiberglass reinforcement. The glass reinforcement is predetermined for each product, and is placed into the mould by a hydraulic press. Then, the resin is injected into the mould under pressure and cured within the mould. The mould is then removed from the mold. This process is a highly effective solution for manufacturing composite parts. The RTM process is highly versatile, and you can tailor your molds to meet the unique needs of your business.