2023-09-01
The DCPD material can be formed into parts with a variety of characteristics, including good tensile strength and good chemical resistance. It is often used to produce large composite fiberglass parts. It is a form of resin transfer molding and can be used to make a variety of parts, including wind turbines and cars. Regardless of the part being made, DCPD molds can provide a high level of efficiency. This makes them a good option for large-scale production.
The DCPD mold process uses a catalyst system that helps accelerate the reaction rate. The catalyst system is split into two parts and then recombined after they have been mixed. It is not stoichiometric, and the ratio is not critical. This makes the process easy and efficient for the manufacturer.
The low viscosity of the liquid components makes it possible to produce parts with large surface areas. They can be up to 13 m2 (120 sq ft) in surface area. They can also weigh several hundred pounds. Production molds are made of aluminum and are generally CNC-machined. Unlike steel molds, aluminum tooling is cheaper and still produces acceptable surfaces. However, if Class A surfaces are required, nickel-plated tooling may be the best choice.
A PDCPD mold can produce high-quality, highly durable, and functional components. Polydicyclopentadiene is a thermoplastic resin that provides excellent strength and a high-quality surface. It can even replace traditional high-impact materials. Its unique properties make it a great choice for custom applications.
A custom mould is a great choice for a business because it makes the process easier and reduces manufacturing errors. A custom mould also allows a company to produce more products in less time. This leads to increased revenues. Furthermore, a custom mould is also less expensive than a standard mould. Finally, custom moulds can be made for a specific product line.
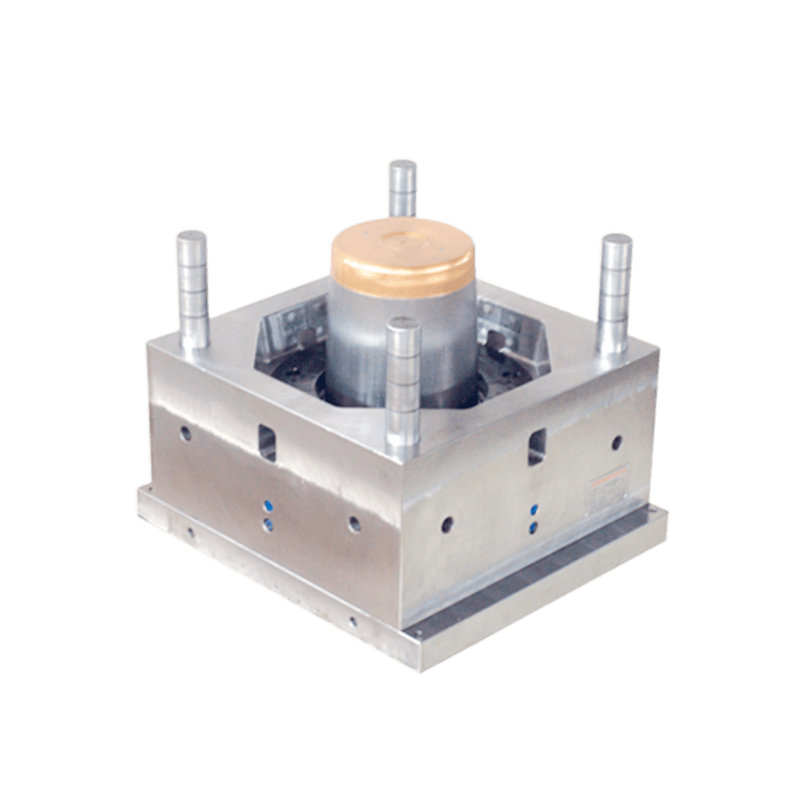