2023-09-01
The RIM PDCPD injection molding process involves the reaction of two liquid precursors - polyol and isocyanate - within a mold cavity. The rapid reaction creates a cross-linked polymer matrix, resulting in a high-strength and impact-resistant part. Unlike traditional injection molding, which mainly utilizes thermoplastics, RIM PDCPD injection molding offers superior mechanical properties and dimensional stability, making it an ideal choice for demanding applications.
One of the key advantages of RIM PDCPD injection molding services is the ability to produce large, complex, and structurally intricate parts. The low viscosity of PDCPD allows it to flow easily within the mold, ensuring uniform filling of intricate geometries, including undercuts, ribs, and thin walls. This versatility in part design opens up new possibilities for engineers and designers, enabling them to create innovative products that would be challenging or impossible to achieve with other manufacturing methods.
RIM PDCPD injection molding services offer exceptional strength-to-weight ratio, making them ideal for applications where lightweight yet durable parts are essential. PDCPD exhibits high tensile and flexural strength, providing excellent mechanical performance while reducing the overall weight of the component. This feature is particularly advantageous in industries such as automotive and transportation, where reducing vehicle weight contributes to fuel efficiency and improved performance.
Chemical resistance is another significant benefit of RIM PDCPD injection molding. PDCPD exhibits exceptional resistance to a wide range of chemicals, including acids, alkalis, and solvents. This makes it an ideal choice for components that come into contact with aggressive substances, such as chemical storage tanks, agricultural equipment, and industrial machinery. The inherent chemical resistance of PDCPD ensures long-term durability and reliability in demanding environments.
RIM PDCPD injection molding services provide excellent corrosion resistance. PDCPD exhibits exceptional resistance to moisture, salt, and environmental factors, making it well-suited for applications in marine, agricultural, and construction industries. The ability to withstand harsh environments ensures the longevity and reliability of the manufactured parts, reducing maintenance costs and enhancing overall performance.
RIM PDCPD injection molding services also offer cost-effective production solutions. The low viscosity of PDCPD allows for quick mold filling, reducing cycle times and increasing production efficiency. Moreover, the ability to produce complex parts in a single step eliminates the need for additional assembly processes, resulting in cost savings and improved production timelines.
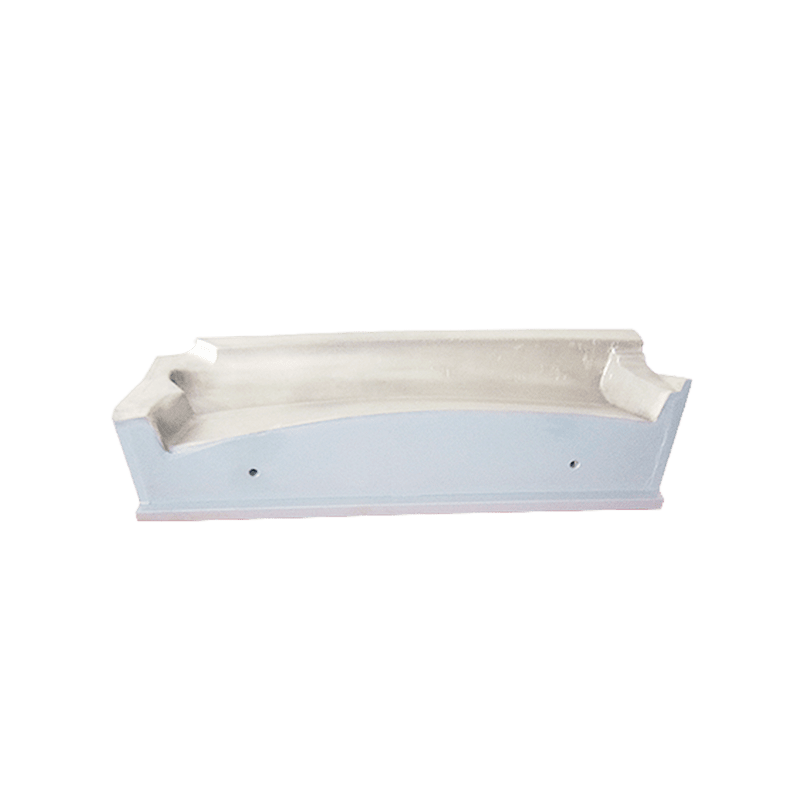