2023-09-01
1. Excellent Mechanical Properties: Rim PDCPD injection molded parts exhibit exceptional mechanical properties, including high strength, impact resistance, and dimensional stability. The material's inherent toughness and rigidity make it suitable for applications that require components to withstand heavy loads, extreme temperatures, and harsh operating conditions.
2. Design Flexibility: Rim PDCPD injection molding offers design flexibility, allowing for the production of complex shapes, intricate details, and precise geometries. The material flows easily during the injection molding process, enabling the creation of parts with varying wall thicknesses, undercuts, and internal features. This flexibility opens up opportunities for innovative designs and customization to meet specific application requirements.
3. Superior Chemical Resistance: PDCPD exhibits excellent chemical resistance, making it suitable for applications that come into contact with various chemicals, solvents, and corrosive substances. Rim PDCPD injection molded parts can withstand exposure to oils, fuels, acids, bases, and industrial chemicals, ensuring long-term performance and durability in challenging environments.
4. High UV Stability: PDCPD materials used in rim injection molding possess high UV stability, making them resistant to fading, discoloration, and degradation caused by prolonged exposure to sunlight. This property is particularly advantageous for outdoor applications where components need to maintain their appearance and performance over extended periods.
5. Cost-Effective Production: Rim PDCPD injection molding offers cost-effective production due to several factors. The low viscosity of PDCPD allows for shorter injection molding cycles, resulting in higher production rates and reduced manufacturing costs. The process also enables efficient material utilization, minimizing waste and optimizing material costs. Additionally, the durability and longevity of PDCPD components contribute to overall cost savings by reducing maintenance, repair, and replacement expenses.
Applications of Rim PDCPD Injection Molding:
1. Automotive Industry: Rim PDCPD injection molding finds extensive applications in the automotive industry. It is used to manufacture exterior body panels, bumpers, fenders, roof systems, and interior components such as instrument panels, door panels, and seat structures. The material's high strength, impact resistance, and design flexibility make it suitable for producing lightweight yet durable components that meet stringent safety and performance requirements.
2. Transportation and Heavy Equipment: Rim PDCPD injection molded parts are utilized in transportation and heavy equipment applications. They are used in the production of truck bodies, agricultural equipment components, construction machinery parts, and railway components. The material's resistance to chemicals, UV stability, and mechanical strength enable it to withstand the demanding conditions encountered in these industries.
3. Electrical and Electronics: Rim PDCPD injection molding is employed in the electrical and electronics sector for manufacturing enclosures, housings, and structural components. The material's electrical insulation properties, flame retardancy, and resistance to environmental factors make it suitable for applications in electrical cabinets, control panels, and electronic enclosures where protection and durability are essential.
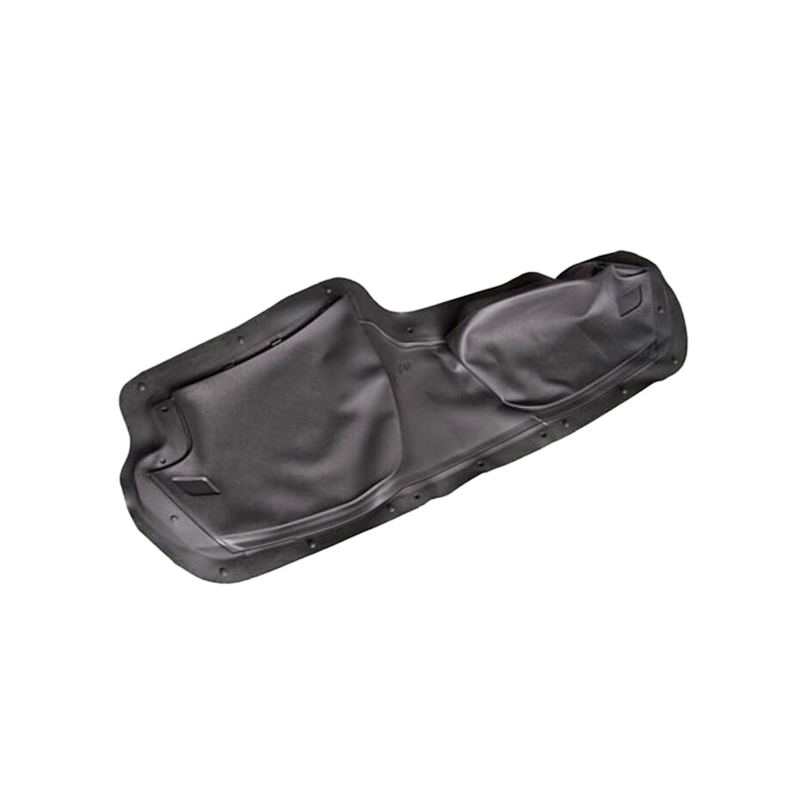