2023-09-01
1. Design Flexibility: Rim PDCPD injection molding allows for complex and intricate part designs. The low viscosity of the liquid resin enables it to flow easily into intricate mold cavities, ensuring precise replication of intricate details and geometries. This flexibility in design opens up possibilities for the production of custom and unique parts that meet specific requirements.
2. Lightweight and High Strength: PDCPD offers an excellent strength-to-weight ratio, making it an ideal choice for applications where lightweight components with high strength are desired. Rim PDCPD injection molding allows the incorporation of reinforcement materials, such as glass fibers, to further enhance the structural integrity and mechanical properties of the final parts.
3. Chemical and Corrosion Resistance: PDCPD exhibits excellent resistance to chemicals, corrosion, and environmental factors. Parts produced through Rim PDCPD injection molding are inherently resistant to a wide range of chemicals, including acids, alkalis, solvents, and automotive fluids. This resistance makes them suitable for applications in industries such as automotive, chemical processing, and agriculture.
4. Impact Resistance: PDCPD possesses exceptional impact resistance, making it suitable for applications that require parts to withstand heavy-duty usage and impacts. This property is particularly valuable in industries like transportation, construction, and material handling, where parts are exposed to challenging conditions and need to withstand frequent impacts or vibration.
5. Dimensional Stability: Rim PDCPD injection molding ensures excellent dimensional stability, producing parts with tight tolerances and minimal warpage. This stability is crucial in applications where precise fit, accuracy, and consistency are required, such as automotive components, enclosures, and structural parts.
Applications of Rim PDCPD Injection Molding:
1. Automotive Industry: Rim PDCPD injection molding finds extensive application in the automotive industry. It is used for producing various components, including body panels, bumpers, fenders, seat structures, interior trim, and under-the-hood parts. The lightweight, high strength, chemical resistance, and impact resistance properties of PDCPD make it suitable for demanding automotive applications.
2. Electrical and Electronics: Rim PDCPD injection molding is utilized in the electrical and electronics industry for manufacturing enclosures, housings, and structural components. The excellent electrical insulation properties of PDCPD, combined with its resistance to chemicals and environmental factors, make it an ideal choice for protecting sensitive electronic components.
3. Industrial Equipment: PDCPD-based parts produced through Rim PDCPD injection molding are used in industrial equipment applications. These include parts for material handling equipment, machinery components, protective covers, and structural supports. The strength, durability, and chemical resistance of PDCPD contribute to the longevity and reliability of industrial equipment.
4. Agricultural and Construction Equipment: Rim PDCPD injection molding is employed in the manufacturing of agricultural and construction equipment parts. Components such as cab structures, fenders, grilles, and hoods benefit from the lightweight, impact resistance, and chemical resistance properties of PDCPD, making them suitable for the demanding conditions in these industries.
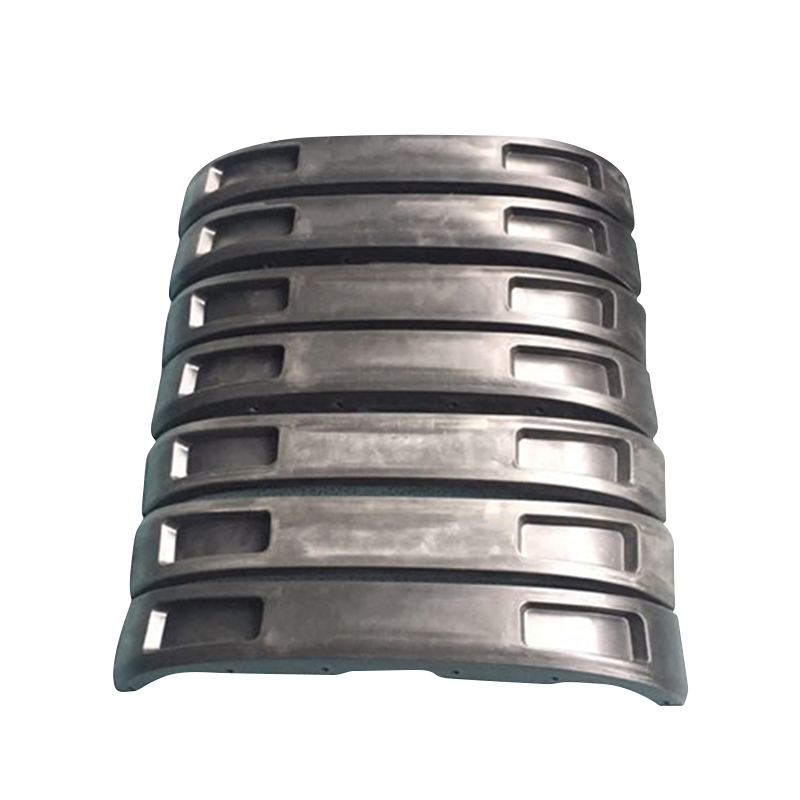