2023-09-01
PDCPD molds enable designers and engineers to achieve intricate shapes, complex geometries, and precise detailing that would be challenging to achieve with other plastics molding processes. PDCPD's low viscosity and high flowability allow it to fill even the most intricate mold cavities, resulting in components with exceptional design flexibility. Manufacturers can produce parts with varying wall thicknesses, undercuts, and integrated features, expanding the possibilities for product innovation and differentiation.
2. Superior Mechanical Properties:
PDCPD molds produce components with superior mechanical properties compared to traditional plastics. PDCPD exhibits excellent impact resistance, high strength-to-weight ratio, and exceptional dimensional stability. These properties make it suitable for applications where structural integrity, durability, and resistance to harsh environments are critical. PDCPD components have found applications in industries such as automotive, construction, agriculture, and industrial equipment.
3. Chemical and Corrosion Resistance:
PDCPD exhibits remarkable resistance to a wide range of chemicals, including acids, bases, solvents, and fuels. This inherent chemical resistance makes PDCPD components ideal for applications where exposure to aggressive substances is prevalent. Additionally, PDCPD's resistance to corrosion ensures long-lasting performance, making it suitable for use in demanding environments.
4. Lightweight and Cost-Effective:
PDCPD molds offer the advantage of lightweight components with excellent strength. The low density of PDCPD enables the production of lightweight parts without compromising on mechanical performance. The lightweight nature of PDCPD components contributes to fuel efficiency, reduced transportation costs, and easier handling during installation. Moreover, PDCPD molds provide a cost-effective solution as they require less material compared to other plastics molding processes, resulting in cost savings.
5. Rapid Production Cycle:
PDCPD molds enable rapid production cycles, making them well-suited for high-volume manufacturing. PDCPD has a fast curing time, allowing for shorter cycle times and increased production rates. This efficiency helps manufacturers meet demanding production schedules and reduce overall lead times, making PDCPD an attractive option for industries with time-sensitive requirements.
6. Durability and Longevity:
PDCPD components exhibit excellent durability and longevity, even in challenging operating conditions. PDCPD's resistance to impact, wear, and weathering ensures that components retain their integrity and functionality over extended periods. This durability translates to reduced maintenance and replacement costs for end-users.
7. Sustainable Manufacturing:
PDCPD molds contribute to sustainable manufacturing practices in several ways. Firstly, PDCPD is a recyclable material, allowing for the reuse and repurposing of waste or scrap material. Secondly, PDCPD molds require lower processing temperatures compared to other plastics molding processes, leading to reduced energy consumption. Finally, the lightweight nature of PDCPD components results in reduced fuel consumption during transportation.
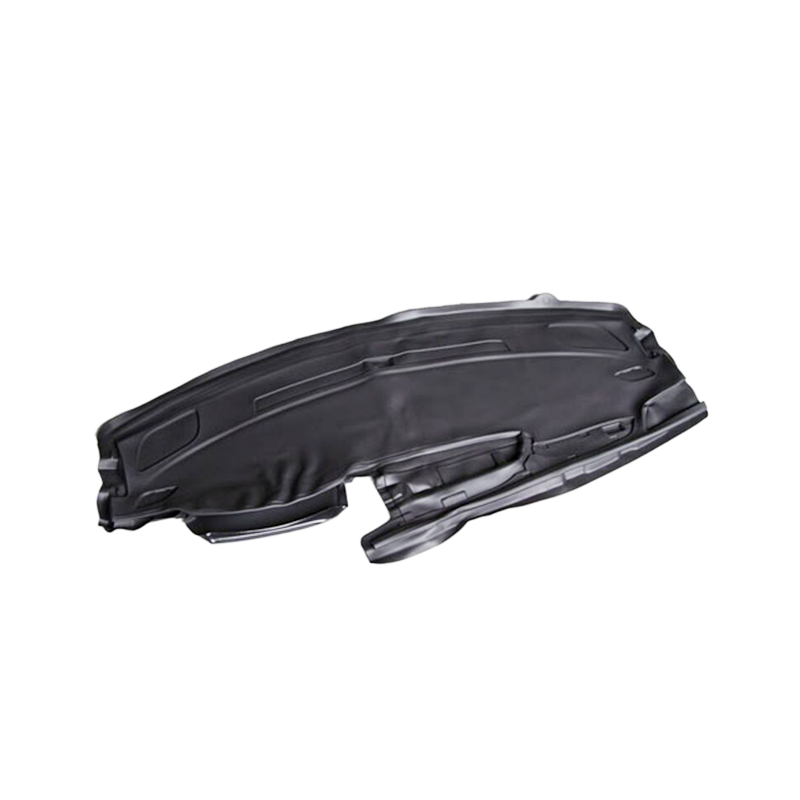