2023-09-01
PDCPD molds offer several advantages over other traditional molding materials:
a. Design Flexibility: PDCPD molds provide excellent design flexibility, allowing for the production of complex and intricate parts. The low viscosity of PDCPD resin enables it to fill intricate mold cavities with ease, resulting in high-precision components. This flexibility allows manufacturers to create customized products and meet specific design requirements.
b. Exceptional Strength and Impact Resistance: PDCPD molds produce parts with exceptional mechanical properties. PDCPD exhibits high tensile strength and impact resistance, making it suitable for applications that require durability and reliability. The molded parts can withstand harsh environments, heavy loads, and extreme temperatures, ensuring long-lasting performance.
c. Chemical and Corrosion Resistance: PDCPD molds offer excellent chemical and corrosion resistance. The molded parts can withstand exposure to various chemicals, solvents, and corrosive substances, making them ideal for applications in industries such as automotive, chemical processing, and marine. This resistance extends the lifespan of the molded components and reduces maintenance costs.
d. Dimensional Stability: PDCPD molds provide excellent dimensional stability, ensuring the accurate reproduction of part dimensions. The low shrinkage characteristics of PDCPD resin minimize post-mold shrinkage, resulting in parts that maintain their intended shape and dimensions over time. This stability is critical for applications that require precise fit and functionality.
e. Heat Resistance: PDCPD molds exhibit high heat resistance, allowing them to withstand elevated temperatures without deformation or loss of mechanical properties. This property makes them suitable for applications in industries such as automotive, electrical, and industrial equipment, where exposure to high temperatures is common.
2. What are the applications of PDCPD molds in the manufacturing industry?
PDCPD molds find diverse applications across various industries:
a. Automotive: PDCPD molds are extensively used in the automotive industry for the production of lightweight, durable, and impact-resistant components. They are employed in applications such as body panels, bumper systems, fenders, engine covers, and structural components. The high strength and dimensional stability of PDCPD molded parts make them ideal for automotive applications.
b. Electrical and Electronics: PDCPD molds are utilized in the electrical and electronics industry for the manufacturing of enclosures, housings, and components. The excellent chemical resistance and electrical insulation properties of PDCPD make it suitable for applications that require protection against moisture, chemicals, and electrical conductivity.
c. Industrial Equipment: PDCPD molds find applications in the production of components for industrial equipment. They are used in manufacturing equipment enclosures, protective covers, machinery components, and structural parts. The combination of strength, impact resistance, and dimensional stability makes PDCPD an ideal choice for industrial equipment applications.
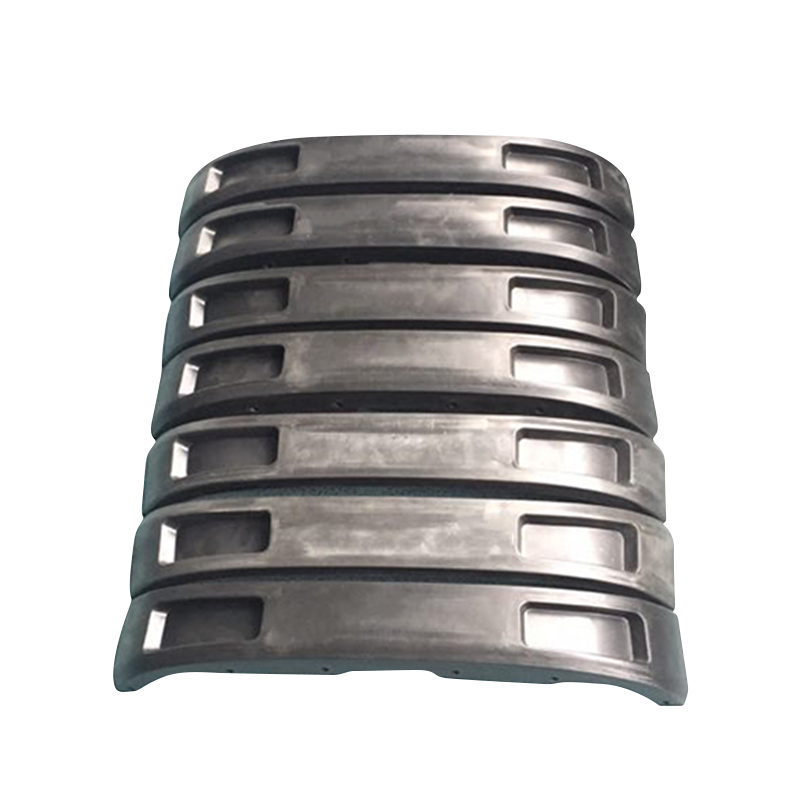